Fine stamping process method of compressor intermediate plate
A process method and compressor technology, applied in the field of compressors, can solve problems such as low efficiency, difficulty in ensuring reliable and stable finished product forming, unfavorable energy conservation and environmental protection, etc.
- Summary
- Abstract
- Description
- Claims
- Application Information
AI Technical Summary
Problems solved by technology
Method used
Image
Examples
Embodiment Construction
[0096] The present invention and its beneficial technical effects will be further described in detail below in conjunction with the accompanying drawings and preferred embodiments. In order to facilitate the distinction during explanation, bolts in the prior art are generally used for “detachable setting”; some similar technical features are divided according to their commonly used size specifications, such as “φ” for diameters and specific numerical values are explained. In practical applications, the corresponding numerical values can be adjusted according to actual needs, and are not fixed. Other components with independent action control that are not specifically described can be driven by conventional methods such as air cylinders and oil cylinders on the punching machine.
[0097] see Figure 27 , the fine blanking process method of the compressor intermediate plate body preferably implemented in the present invention is characterized in that it includes the followi...
PUM
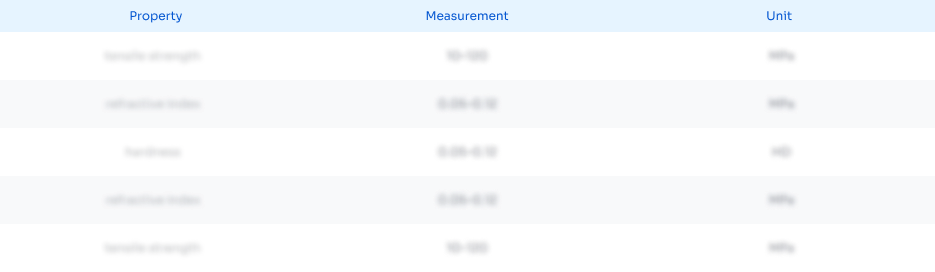
Abstract
Description
Claims
Application Information

- R&D Engineer
- R&D Manager
- IP Professional
- Industry Leading Data Capabilities
- Powerful AI technology
- Patent DNA Extraction
Browse by: Latest US Patents, China's latest patents, Technical Efficacy Thesaurus, Application Domain, Technology Topic, Popular Technical Reports.
© 2024 PatSnap. All rights reserved.Legal|Privacy policy|Modern Slavery Act Transparency Statement|Sitemap|About US| Contact US: help@patsnap.com