Hard chromium electroplating process
An electroplating process and hard chrome technology, applied in the field of hard chrome electroplating process, can solve the problems of water consumption, poor adhesion between the coating and the substrate, and the electroplating process is not environmentally friendly enough to achieve the effect of maintaining secondary utilization and promoting filtration
- Summary
- Abstract
- Description
- Claims
- Application Information
AI Technical Summary
Problems solved by technology
Method used
Image
Examples
Embodiment approach
[0037] As an embodiment of the present invention, a tensioning wheel 5 is provided above the servo motor 12, and the tensioning wheel 5 includes a roller 51 and an elastic strut 52; the elastic strut 52 is installed on the column 112, and the elastic strut The two ends of bar 52 are provided with the roller 51 of rotatable installation; Said roller 51 and servomotor 12 contact with the belt that disc 4 transmission is connected; The distance between them changes, and the belt connected by its transmission is also disturbed, which affects the rotation of the servo motor 12 driving the disc 4; through the roller 51 and the elastic pole 52 arranged on the column 112, the belt is in a stable tension. In the tight state, after the height of the disc 4 on the column 112 is changed, and the belt is in the process of relaxation, the distance between the rollers 51 is increased through the elastic strut 52 to keep the belt driven between the servo motor 12 and the disc 4 in a stable sta...
PUM
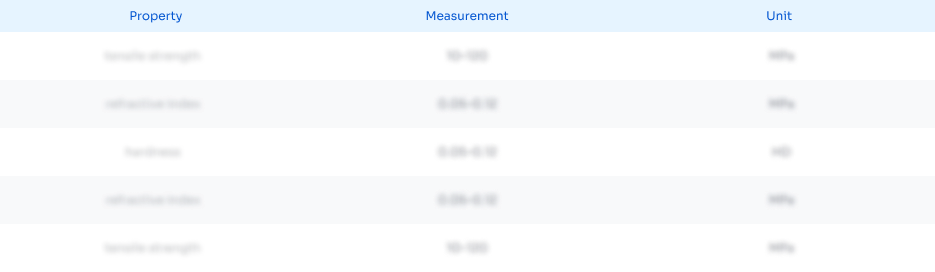
Abstract
Description
Claims
Application Information

- Generate Ideas
- Intellectual Property
- Life Sciences
- Materials
- Tech Scout
- Unparalleled Data Quality
- Higher Quality Content
- 60% Fewer Hallucinations
Browse by: Latest US Patents, China's latest patents, Technical Efficacy Thesaurus, Application Domain, Technology Topic, Popular Technical Reports.
© 2025 PatSnap. All rights reserved.Legal|Privacy policy|Modern Slavery Act Transparency Statement|Sitemap|About US| Contact US: help@patsnap.com