Nylon elastomer material and preparation method thereof
A technology of nylon elastomer and nylon, which is applied in the field of nylon materials, can solve problems such as difficult to meet the application, sports shoe soles are not light enough, sports shoe soles are not comfortable, etc., and achieve the effect of improving thermal stability, transparency and flexibility.
- Summary
- Abstract
- Description
- Claims
- Application Information
AI Technical Summary
Problems solved by technology
Method used
Image
Examples
Embodiment 1
[0018] Embodiment 1: a kind of preparation method of nylon elastomer material, its method is as follows:
[0019] With 5kg nylon 1012 salt monomer, 1kg softening agent dimer acid, 0.2kg end-capping agent dodecyl diamine and auxiliary agent namely 10g catalyst sodium ethylate and ammonium salt i.e. dodecyltrimethylammonium chloride, resist Add oxygen agent 1098, heat stabilizer HT-26, heat stabilizer CS-181, and 2kg of solvent water into the polymerization kettle, stir at a speed of 40r / min, raise the temperature to 240°C, and pressure to 1.5MPa, react for 2 hours, and drop to normal Then keep the negative pressure to -0.1MPa for 2 hours. The alcohol produced by condensation during polymerization is recovered through rectification and three-stage condensation, and finally pressurized and extruded, cooled, granulated or diced, dried, and packaged. After granulation or granulation, the unqualified products after screening are returned to the polymerization kettle, and vacuum dryi...
Embodiment 2
[0021] A kind of preparation method of nylon elastomer material, its method is as follows:
[0022] With 5kg nylon 1012 salt monomer, 1kg softening agent polytetramethylene glycol, 0.9kg end-capping agent dodecane dibasic acid and auxiliary agent namely 15g catalyst magnesium chloride, 10g antioxidant 1098 and heat stabilizer HT-181, 2kg water Add to the polymerization kettle, stir at the speed of 40r / min, raise the temperature to 240°C, and the pressure to 1.5MPa, react for 2h, drop to normal pressure, then vacuumize to negative pressure -0.1MPa, continue for 2h, and condense the alcohol produced during polymerization Alcohol is recovered through rectification and three-stage condensation, and finally pressurized and extruded, cooled, granulated or diced, dried, packaged, and unqualified products after granulated or diced are returned to the polymerization kettle, and vacuum drying is used for drying , to obtain the final finished nylon elastomer material.
Embodiment 3
[0024] A kind of preparation method of nylon elastomer material, its method is as follows:
[0025] 5kg nylon 1012 salt monomer, 0.8kg softening agent double-ended hydroxypolytetramethyl ether, 0.5kg end-capping agent adipic dibasic acid and auxiliary agent, namely 15g catalyst sodium ethylate, 10g antioxidant 1098 and heat stabilizer Add HT-26, 2kg of water into the polymerization kettle, stir at a speed of 40r / min, raise the temperature to 240°C, and the pressure to 1.5MPa, react for 2h, drop to normal pressure, and then evacuate to negative pressure -0.1MPa for 2h , the alcohol produced by condensation during polymerization is recovered through rectification and three-stage condensation, and finally pressurized and extruded, cooled, granulated or granulated, dried, packaged, and unqualified products are screened and returned to polymerization after granulated or granulated Still, drying adopts vacuum drying to obtain the final finished nylon elastomer material.
[0026] Am...
PUM
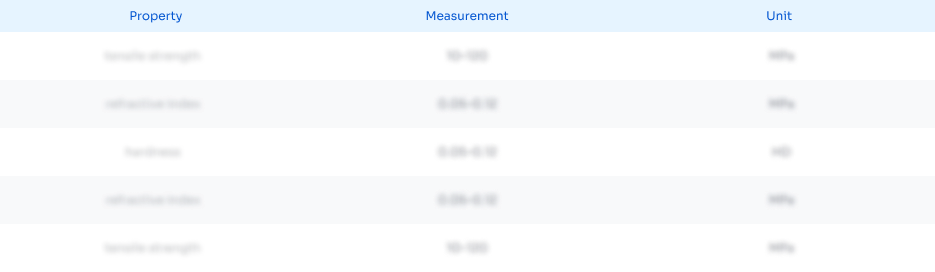
Abstract
Description
Claims
Application Information

- R&D
- Intellectual Property
- Life Sciences
- Materials
- Tech Scout
- Unparalleled Data Quality
- Higher Quality Content
- 60% Fewer Hallucinations
Browse by: Latest US Patents, China's latest patents, Technical Efficacy Thesaurus, Application Domain, Technology Topic, Popular Technical Reports.
© 2025 PatSnap. All rights reserved.Legal|Privacy policy|Modern Slavery Act Transparency Statement|Sitemap|About US| Contact US: help@patsnap.com