Preparation method of high-efficiency composite wood fire retardant
A compound type, flame retardant technology, applied in wood treatment, impregnated wood, wood impregnation, etc., can solve the problems of poor flame retardant and smoke suppression effects, unsatisfactory compatibility, dripping, etc., to achieve good flame retardant Combustion synergistic effect, mechanical performance improvement, and the effect of reducing combustion speed
- Summary
- Abstract
- Description
- Claims
- Application Information
AI Technical Summary
Problems solved by technology
Method used
Image
Examples
Embodiment 1
[0029] A preparation method of a high-efficiency composite wood flame retardant is: cetyltrimethylammonium bromide, sodium dodecylsulfonate, polystyrene-b-polyacrylic acid in a weight ratio of 5:5:1 The composite template agent was added to a solution of water, diethyl ether, and ethanol at a mass ratio of 5:1:4, stirred and dissolved, and then NaOH solution with a mass concentration of 33% was added, and after stirring for 15 minutes, tetrasilicic acid was added dropwise. Ethyl ester, after reacting at room temperature for 10 hours, transferred to a polytetrafluoroethylene bottle, placed in a water bath at 85°C for 28 hours, filtered, washed with water until neutral, then rinsed with acetone, transferred to a flask and reduced by a rotary evaporator at 35°C dried under pressure to obtain mesoporous SiO 2 ; the mesoporous SiO 2 Add it into deionized water and ultrasonically vibrate to make a suspension, add antimony trichloride into concentrated hydrochloric acid, stir to dis...
Embodiment 2
[0031] A preparation method of a high-efficiency composite wood flame retardant is: cetyltrimethylammonium bromide, sodium dodecylsulfonate, polystyrene-b-polyacrylic acid in a weight ratio of 5:5:1 The composite template agent was added to a solution of water, diethyl ether, and ethanol in a mass ratio of 5:1:4, stirred and dissolved, and then NaOH solution with a mass concentration of 30% was added. After stirring for 10 minutes, tetrasilicic acid was added dropwise. Ethyl ester, after reacting at room temperature for 12 hours, transferred to a polytetrafluoroethylene bottle, placed in a water bath at 88°C and sealed for 26 hours, filtered, washed with water until neutral, then rinsed with acetone, transferred to a flask and reduced to 30°C with a rotary evaporator. dried under pressure to obtain mesoporous SiO 2; the mesoporous SiO 2 Add it into deionized water and ultrasonically vibrate to make a suspension, add antimony trichloride into concentrated hydrochloric acid, st...
Embodiment 3
[0033] A preparation method of a high-efficiency composite wood flame retardant is: cetyltrimethylammonium bromide, sodium dodecylsulfonate, polystyrene-b-polyacrylic acid in a weight ratio of 5:5:1 The composite template agent was added to a solution of water, diethyl ether, and ethanol at a mass ratio of 5:1:4, stirred and dissolved, and then NaOH solution with a mass concentration of 35% was added. After stirring for 20 minutes, tetrasilicic acid was added dropwise. Ethyl ester, after reacting at room temperature for 10 hours, transferred to a polytetrafluoroethylene bottle, placed in a water bath at 85°C for 25 hours, filtered, washed with water until neutral, then rinsed with acetone, transferred to a flask and reduced to 30°C with a rotary evaporator. dried under pressure to obtain mesoporous SiO 2 ; the mesoporous SiO 2 Add it into deionized water and ultrasonically vibrate to make a suspension, add antimony trichloride into concentrated hydrochloric acid, stir to diss...
PUM
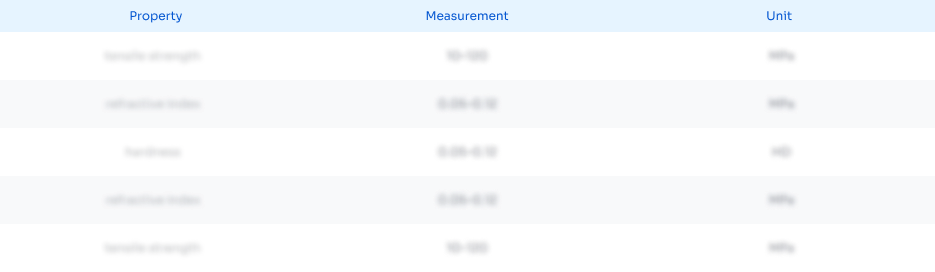
Abstract
Description
Claims
Application Information

- R&D
- Intellectual Property
- Life Sciences
- Materials
- Tech Scout
- Unparalleled Data Quality
- Higher Quality Content
- 60% Fewer Hallucinations
Browse by: Latest US Patents, China's latest patents, Technical Efficacy Thesaurus, Application Domain, Technology Topic, Popular Technical Reports.
© 2025 PatSnap. All rights reserved.Legal|Privacy policy|Modern Slavery Act Transparency Statement|Sitemap|About US| Contact US: help@patsnap.com