Comprehensive recovery method using zinc volatilized kiln slag as fuel
A recovery method and zinc volatilization technology, applied in the field of comprehensive recovery using zinc volatilized kiln slag as fuel, can solve problems such as poor economy, occupation of land resources, pollution, etc., and achieve the effects of solving environmental protection problems, simple process flow, and energy saving
- Summary
- Abstract
- Description
- Claims
- Application Information
AI Technical Summary
Problems solved by technology
Method used
Image
Examples
Embodiment 1
[0026] Zinc volatilization slag (main components Zn 1.56%; Cu 1.16%; Pb 0.48%; Fe 24.08%; S 4.74; Ag 225g / t; SiO 2 13.72; CaO 5.06%; MgO 2.29%; C 25%; calorific value 7500KJ / kg); copper concentrate (mainly composed of Cu24.95%; Fe 27.04%; S 33.72%; SiO 2 3.80%; CaO 0.28%; Pb 0.34%; Zn 1.32%; Ag 383.3g / t; As 0.30%; Bi 0.06%; Sb 0.06%; Al 2 o 3 1.52%; MgO 0.48%; F 0.02%); slagging agent quartz stone contains SiO 2 85%; limestone contains 50% CaO.
[0027] 1. Mixing materials: Zinc volatilization kiln slag, copper concentrate, pulverized coal, quartz stone, and limestone are stored in their own feeding bins, and the feeding belt of the feeding bin is equipped with a feeder to control the weight to adjust the feeding speed. Zinc volatilization kiln slag, quartz stone and limestone are mixed according to the proportions of 15%, 5.4% and 2.3% of the copper concentrate by weight respectively, and the zinc volatilization kiln slag, pulverized coal and copper concentrate are first s...
Embodiment 2
[0035] Zinc volatilization slag (main components Zn 1.56%; Cu 1.16%; Pb 0.48%; Fe 24.08%; S 4.74; Ag 225g / t; SiO 2 13.72; CaO 5.06%; MgO 2.29%; C 25%; calorific value 7500KJ / kg); copper concentrate (Cu 24.95%; Fe27.04%; S 33.72%; SiO 2 3.80%; CaO 0.28%; Pb 0.34%; Zn 1.32%; Ag 383.3g / t; As 0.30%; Bi 0.06%; Sb 0.06%; Al 2 o 3 1.52%; MgO 0.48%; F 0.02%); slagging agent quartz stone contains SiO 2 85%; limestone contains 50% CaO.
[0036] 1. Mixing materials: Zinc volatilization kiln slag, copper concentrate, pulverized coal, quartz stone, and limestone are stored in their own feeding bins, and the feeding belt of the feeding bin is equipped with a feeder to control the weight to adjust the feeding speed. Zinc volatilization kiln slag, quartz stone and limestone are mixed according to the proportions of 15%, 5.4% and 2.3% of the copper concentrate by weight respectively, and the zinc volatilization kiln slag, pulverized coal and copper concentrate are first sent into the dis...
PUM
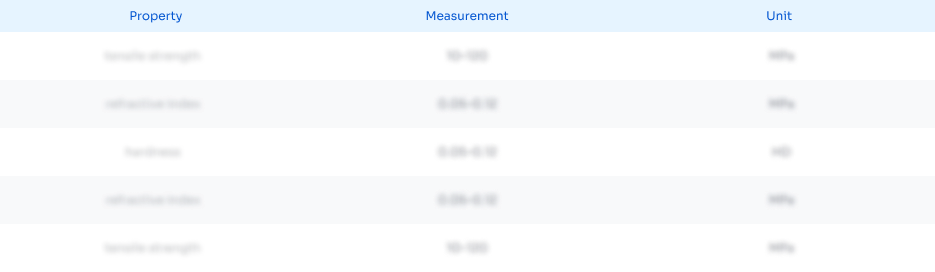
Abstract
Description
Claims
Application Information

- Generate Ideas
- Intellectual Property
- Life Sciences
- Materials
- Tech Scout
- Unparalleled Data Quality
- Higher Quality Content
- 60% Fewer Hallucinations
Browse by: Latest US Patents, China's latest patents, Technical Efficacy Thesaurus, Application Domain, Technology Topic, Popular Technical Reports.
© 2025 PatSnap. All rights reserved.Legal|Privacy policy|Modern Slavery Act Transparency Statement|Sitemap|About US| Contact US: help@patsnap.com