Epoxy self-leveling antistatic topcoat and preparation method thereof
A self-leveling and antistatic technology, applied in epoxy resin coatings, conductive coatings, coatings, etc., can solve problems such as being susceptible to friction or impact, reduced electrical conductivity, and ignition of explosives, so as to avoid safety accidents and structural Increased strength and good electrical conductivity
- Summary
- Abstract
- Description
- Claims
- Application Information
AI Technical Summary
Problems solved by technology
Method used
Image
Examples
Embodiment 1
[0053] Embodiment 1: An epoxy self-leveling antistatic topcoat, including A component and B component that are stored separately and mixed in a ratio of 5:1 by weight when used, each component raw material and its corresponding The parts by weight are shown in Table 1, and are prepared through the following steps:
[0054] Step 1: Mix bisphenol A type epoxy resin, reactive diluent AGE and benzyl alcohol in corresponding parts by weight, then stir for 15 minutes at a speed of 300rpm, and continue to add Disponer 9250 wetting and dispersing agent in corresponding parts by weight, poly Methyl siloxane, polyacrylic acid and epoxy color paste, after continuous stirring for 7.5 minutes, then add wax powder and organobentonite in corresponding parts by weight, disperse at high speed for 15 minutes, stirring speed is 700rpm, continue to add silicon powder in corresponding parts by weight For barium powder, the stirring speed was increased to 1500rpm, and the high-speed dispersion was ...
Embodiment 2
[0061] Embodiment 2: A kind of epoxy self-leveling antistatic surface coating, differs from Embodiment 1 in that it specifically includes the following steps:
[0062] Step 1: Mix bisphenol A type epoxy resin, reactive diluent AGE and benzyl alcohol in corresponding parts by weight, then stir at 200rpm for 20min, continue to add Disponer 9250 wetting and dispersing agent in corresponding parts by weight, poly Methyl siloxane, polyacrylic acid and epoxy color paste, after stirring continuously for 10 minutes, then add wax powder and organobentonite in corresponding parts by weight, disperse at high speed for 10 minutes, stirring speed is 800rpm, continue to add silicon barium in corresponding parts by weight powder, increase the stirring speed to 1800rpm, and disperse at high speed for 50 minutes to obtain a slurry;
[0063] Step 2: Grind the slurry obtained in Step 1 to a fineness of 50 μm, then add corresponding parts by weight of epoxy color paste, disperse at a high speed f...
Embodiment 3
[0066] Embodiment 3: An epoxy self-leveling antistatic topcoat, which differs from Embodiment 1 in that it specifically includes the following steps:
[0067] Step 1: Mix bisphenol A type epoxy resin, reactive diluent AGE and benzyl alcohol in corresponding parts by weight, then stir for 10 minutes at a speed of 400rpm, and continue to add Disponer 9250 wetting and dispersing agent, polydimethylsiloxane in corresponding parts by weight Methylsiloxane, polyacrylic acid and epoxy color paste, after stirring continuously for 5 minutes, then add wax powder and organobentonite in corresponding parts by weight, disperse at high speed for 20 minutes, stirring speed is 600rpm, continue to add silicon barium in corresponding parts by weight powder, increase the stirring speed to 1200rpm, and disperse at high speed for 80min to obtain a slurry;
[0068] Step 2: Grind the slurry obtained in Step 1 to a fineness of 40 μm, then add epoxy color paste in corresponding parts by weight, disper...
PUM
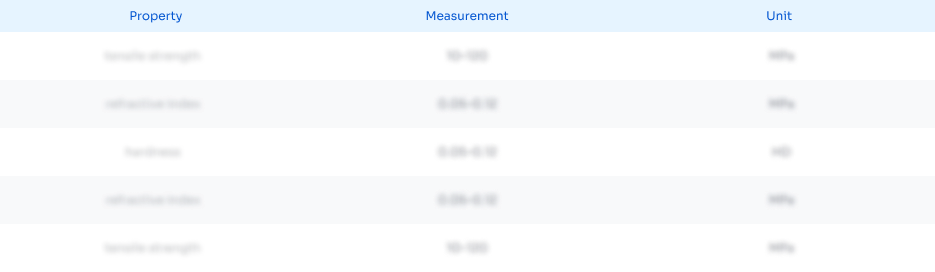
Abstract
Description
Claims
Application Information

- R&D
- Intellectual Property
- Life Sciences
- Materials
- Tech Scout
- Unparalleled Data Quality
- Higher Quality Content
- 60% Fewer Hallucinations
Browse by: Latest US Patents, China's latest patents, Technical Efficacy Thesaurus, Application Domain, Technology Topic, Popular Technical Reports.
© 2025 PatSnap. All rights reserved.Legal|Privacy policy|Modern Slavery Act Transparency Statement|Sitemap|About US| Contact US: help@patsnap.com