Method for preparing 1, 3-cyclohexanediamine by hydrogenation of m-xylylenediamine
A technology of m-xylylenediamine and cyclohexyldimethylamine, which is applied to the hydrogenation of m-xylylenediamine to prepare 1,3-cyclohexanedimethylamine, and the hydrogenation of high-concentration m-xylylenediamine to prepare high-cis isomers In the field of 1,3-cyclohexanedimethylamine content, it can solve the problems of low production efficiency per unit volume of reactor, high energy consumption for product separation, and low concentration of hydrogenation substrate, which is beneficial to scale-up and industrial implementation, improves production efficiency, and reduces Effect of Solvent Dosage
- Summary
- Abstract
- Description
- Claims
- Application Information
AI Technical Summary
Problems solved by technology
Method used
Examples
Embodiment 1
[0038] In a 2L autoclave, add 100g THF, 6g catalyst sample, 0.04g 2-picoline, put on the autoclave, exhaust the air in the autoclave with low-pressure nitrogen and hydrogen successively for 3 times, then fill with hydrogen to 3MPa, and raise the temperature to 120°C , pressurize again to 8.0MPa, adjust the stirring rate to be 1000rpm, open the m-xylylenediamine feed pump feed, the feed time is 3h, the total feed amount of m-xylylenediamine is 300g (that is, the feed rate is 100g / h), feed the material, continue to stir the reaction for 1h, stop stirring, close the hydrogen inlet valve, cool down, discharge the residual gas in the kettle, use the built-in filter to filter out the reaction mother liquor, utilize gas chromatography to carry out external standard quantitative analysis, and obtain the intermediate The conversion rate of xylylenediamine was 99.8%, the selectivity of 1,3-cyclohexanedimethylamine was 97.5%, the molar yield was 97.3%, and the cis-isomer / trans-isomer rat...
Embodiment 2
[0040] In a 2L autoclave, add 100g of 1,3-cyclohexanedimethylamine, 15g of catalyst sample, 3g of 3-methylquinoline, put on the autoclave, exhaust the air in the autoclave with low-pressure nitrogen and hydrogen successively for 3 times, and refill the autoclave. Hydrogen to 3MPa, heat up to 100°C, pressurize again to 12MPa, adjust the stirring rate to 1000rpm, turn on the m-xylylenediamine feed pump to feed, the feed time is 4h, and the total feed amount of m-xylylenediamine is 400g (that is, the feed rate is 100g / h), after feeding the material, continue to stir and react for 0.8h, stop stirring, close the hydrogen inlet valve, cool down, discharge the residual gas in the kettle, use a built-in filter to filter out the reaction mother liquor, and use gas chromatography Quantitative analysis of external standard was carried out to obtain m-xylylenediamine conversion rate of 99.6%, 1,3-cyclohexanedimethylamine selectivity of 96.8%, molar yield of 96.4%, cis-isomer / trans-isomer r...
Embodiment 3
[0042] In a 2L autoclave, add 90g THF, 3g catalyst sample, and 0.02g quinoline, put on the autoclave, exhaust the air in the autoclave with low-pressure nitrogen and hydrogen successively for 3 times, then fill with hydrogen to 3MPa, heat up to 90°C, and increase the temperature. Press down to 14MPa, adjust the stirring rate to be 1000rpm, open the m-xylylenediamine feed pump feed, the feed time is 7.5h, and the total feed amount of m-xylylenediamine is 450g (that is, the feed rate is 60g / h) , feed the material, continue to stir and react for 3.0h, stop stirring, close the hydrogen inlet valve, cool down, discharge the residual gas in the kettle, filter the reaction mother liquor with a built-in filter, and use gas chromatography to carry out external standard quantitative analysis to obtain m-phenylene The conversion rate of methylamine was 99.4%, the selectivity of 1,3-cyclohexanedimethylamine was 96.5%, the molar yield was 95.9%, and the cis-isomer / trans-isomer ratio was 81 / ...
PUM
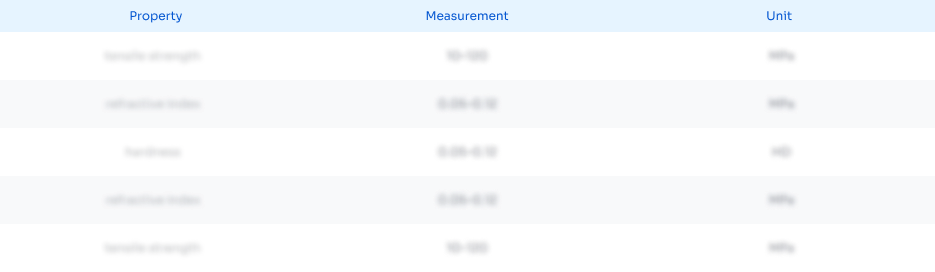
Abstract
Description
Claims
Application Information

- Generate Ideas
- Intellectual Property
- Life Sciences
- Materials
- Tech Scout
- Unparalleled Data Quality
- Higher Quality Content
- 60% Fewer Hallucinations
Browse by: Latest US Patents, China's latest patents, Technical Efficacy Thesaurus, Application Domain, Technology Topic, Popular Technical Reports.
© 2025 PatSnap. All rights reserved.Legal|Privacy policy|Modern Slavery Act Transparency Statement|Sitemap|About US| Contact US: help@patsnap.com