Ultralow-temperature-resistant environment-friendly two-component polyurethane adhesive and preparation and application thereof
A two-component polyurethane, environmentally friendly technology, used in polyurea/polyurethane adhesives, adhesives, non-polymer adhesive additives, etc., can solve the problems of slow curing speed, non-environmentally friendly solvents, and low peel strength , to achieve the effect of fast curing speed, improved peel strength, good hydrolysis resistance and low temperature peel strength
- Summary
- Abstract
- Description
- Claims
- Application Information
AI Technical Summary
Problems solved by technology
Method used
Examples
Embodiment 1
[0056] A component comprises the component of following percentage by weight:
[0057] Isocyanate (Wanhua MDI-100) 40%
[0058] Polyether polyol (Dow Chemical 1000LM) 10%
[0059] Castor oil polyol (Japan Ito Oil H-30) 50%
[0060] Mix the above components A evenly, then raise the temperature to 75~80°C and react for 3 hours, vacuumize to remove bubbles, cool down and discharge, and then the A-1 component is obtained.
[0061] B component comprises the component of following percentage by weight:
[0062] Polypropylene carbonate polyol (Dazhi Fine Chemical PPC-2202P) 5%
[0063] Modified polytetrahydrofuran polyol (Invista 3MCPG) 53.5%
[0064] Castor oil polyol (Japan Ito Oil H-30) 5%
[0065] Cross-linking agent (USA Eastman TMPD) 3%
[0066] Catalyst (U.S. leading chemical BiCAT 8108) 0.5%
[0067] Latent curing agent (Incorez EH, UK) 1%
[0068] Adhesion promoter (Hanjiang Fine Chemical JH-0187) 2%
[0069] Filler (Jiangxi Huaming Nano Calcium Carbonate SPTL-2) 20...
Embodiment 2
[0074] A component comprises the component of following percentage by weight:
[0075] Isocyanate (Wanhua MDI-100) 40%
[0076] Polyether polyol (Dow Chemical 1000LM) 40%
[0077] Castor oil polyol (Japan Ito Oil H-30) 20%
[0078] Mix the above-mentioned component A evenly, then raise the temperature to 75~80°C and react for 3 hours, vacuumize to remove foam, cool down and discharge the material, and then the A-2 component is obtained.
[0079] B component comprises the component of following percentage by weight:
[0080] Polypropylene carbonate polyol (Dazhi Fine Chemical PPC-2202P) 25%
[0081] Modified polytetrahydrofuran polyol (Invista 3MCPG) 16.4%
[0082] Castor oil polyol (Japan Ito Oil H-30) 25%
[0083] Cross-linking agent (USA Eastman TMPD) 5%
[0084] Catalyst (U.S. leading chemical BiCAT 8108) 1%
[0085] Latent curing agent (Incorez EH, UK) 0.6%
[0086] Adhesion promoter (Hanjiang Fine Chemical JH-0187) 2%
[0087] Filler (Jiangxi Huaming Nano Calcium...
Embodiment 3
[0092] A component comprises the component of following percentage by weight:
[0093] Isocyanate (Wanhua MDI-100) 55%
[0094] Polyether polyol (Dow Chemical 1000LM) 10%
[0095] Castor oil polyol (Japan Ito Oil H-30) 35%
[0096] Mix the above-mentioned components A evenly, then raise the temperature to 75~80°C and react for 3 hours, vacuumize to remove bubbles, cool down and discharge the material, and then the A-3 component is obtained.
[0097] B component comprises the component of following percentage by weight:
[0098] Polypropylene carbonate polyol (Dazhi Fine Chemical PPC-2202P) 40%
[0099] Modified polytetrahydrofuran polyol (Invista 3MCPG) 7.4%
[0100] Castor oil polyol (Japan Ito Oil H-30) 30%
[0101] Cross-linking agent (USA Eastman TMPD) 3%
[0102] Catalyst (U.S. leading chemical BiCAT 8108) 1%
[0103] Latent curing agent (Incorez EH, UK) 0.6%
[0104] Adhesion promoter (Hanjiang Fine Chemical JH-0187) 3%
[0105] Filler (Jiangxi Huaming Nano Calc...
PUM
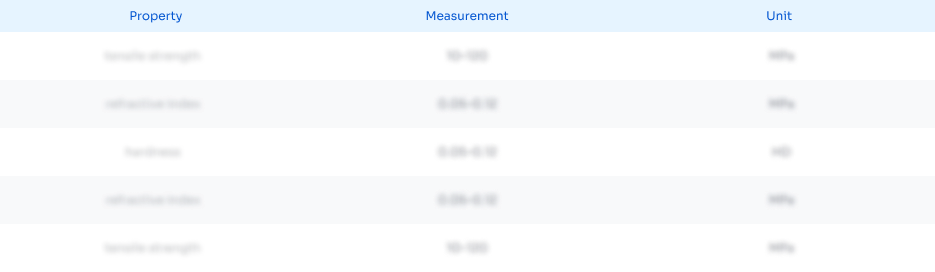
Abstract
Description
Claims
Application Information

- R&D Engineer
- R&D Manager
- IP Professional
- Industry Leading Data Capabilities
- Powerful AI technology
- Patent DNA Extraction
Browse by: Latest US Patents, China's latest patents, Technical Efficacy Thesaurus, Application Domain, Technology Topic, Popular Technical Reports.
© 2024 PatSnap. All rights reserved.Legal|Privacy policy|Modern Slavery Act Transparency Statement|Sitemap|About US| Contact US: help@patsnap.com