Method for preparing CuTi alloy material by vacuum induction melting
A technology of vacuum induction melting and alloy materials, which is applied in the field of preparation of vacuum induction melting CuTi alloy materials. The effect of speed and easy control
- Summary
- Abstract
- Description
- Claims
- Application Information
AI Technical Summary
Problems solved by technology
Method used
Image
Examples
Embodiment
[0028] A preparation method for vacuum induction melting CuTi alloy material, comprising the following steps:
[0029] (1) Ingredients, by weight percentage, the percentage content of each element in the raw material is: Ti3.6%, Cu96.4%, wherein Ti is added in the form of CuTi50 master alloy, and the master alloy and electrolytic copper plate are weighed in proportion;
[0030] (2) Install the furnace, open the vent valve, open the furnace cover, put the steel mold on the upper part of the steel mold and put the insulation riser, wrap the insulation cotton on the outer wall of the steel mold, set up the chute, and the chute hole is aligned with the center of the steel mold, Put a gasket at the bottom of the steel mold to prevent breakdown, install the electrolytic copper plate first, intersperse the CuTi50 intermediate alloy on the top of the electrolytic copper plate, close the furnace cover, clean the observation window, and close the air release valve;
[0031] (3) Vacuumiz...
PUM
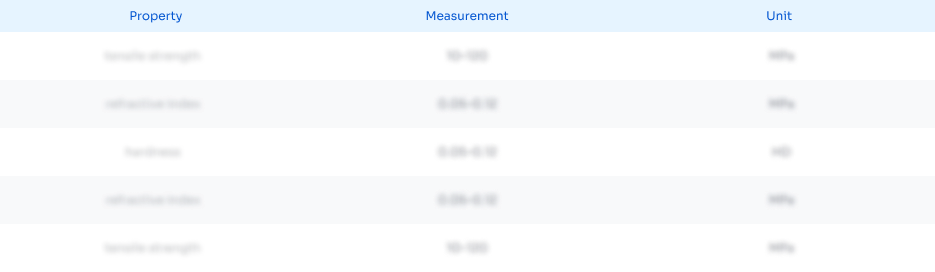
Abstract
Description
Claims
Application Information

- Generate Ideas
- Intellectual Property
- Life Sciences
- Materials
- Tech Scout
- Unparalleled Data Quality
- Higher Quality Content
- 60% Fewer Hallucinations
Browse by: Latest US Patents, China's latest patents, Technical Efficacy Thesaurus, Application Domain, Technology Topic, Popular Technical Reports.
© 2025 PatSnap. All rights reserved.Legal|Privacy policy|Modern Slavery Act Transparency Statement|Sitemap|About US| Contact US: help@patsnap.com