Method for treating waste liquid containing magnesium and/or calcium in rare earth smelting separation course
A separation process, rare earth technology, applied in chemical instruments and methods, magnesium oxide, chlorine/hydrogen chloride, etc., can solve the problems of low activity, slow reaction speed, incomplete reaction, etc., achieve shortened process flow, loose pyrolysis conditions, The effect of reducing sales pressure
- Summary
- Abstract
- Description
- Claims
- Application Information
AI Technical Summary
Problems solved by technology
Method used
Image
Examples
Embodiment 1
[0052] Take the magnesium chloride wastewater solution with a concentration of 2.20mol / L produced in the rare earth smelting process, concentrate it to a magnesium chloride concentration of 530g / L, and then put it into a spray pyrolysis furnace for pyrolysis. The pyrolysis temperature is 600°C and the pyrolysis time is 2h. Magnesium oxide solid and gas containing hydrogen chloride, the purity of magnesium oxide is 95.0%, the gas containing hydrogen chloride is dedusted by cyclone and then absorbed by dilute hydrochloric acid to produce 20% hydrochloric acid, which is returned to the rare earth extraction and separation process as the acid for stripping.
[0053] Magnesium oxide solids were prepared by pulping and carbonization to obtain pure magnesium bicarbonate solution with a concentration of 11.5g / L. The magnesium bicarbonate solution was pretreated with 1.50mol / L P204 organic phase in comparison with O / A=1.11:1 to obtain a solution containing Magnesium-loaded organic, afte...
Embodiment 2
[0058] Take the 1.35mol / L magnesium chloride wastewater solution produced in the rare earth smelting process, concentrate it to a magnesium chloride concentration of 540g / L, spray and dehydrate it at 120°C to obtain hydrated magnesium chloride, and then add it to a fluidized bed pyrolysis furnace for pyrolysis. The temperature is 550°C, and the pyrolysis time is 1 hour to obtain solid magnesium oxide and gas containing hydrogen chloride. The purity of magnesium oxide is 92.5%.
[0059] The magnesium oxide solid, 1.40mol / L P507 organic phase and 0.90mol / L neodymium chloride solution are mixed for pre-extraction, the solid-liquid ratio of magnesium oxide solid to P507 organic phase is 1:104, and the P507 organic phase and neodymium chloride solution phase Ratio O / A=5.2:1, the obtained neodymium-containing loaded organic is used for the extraction and separation of neodymium samarium mixed rare earth feed liquid, and the relative content of impurities in the output neodymium chlor...
Embodiment 3
[0064] Take the 0.45mol / L magnesium chloride wastewater solution produced in the rare earth smelting process, concentrate it to a magnesium chloride concentration of 450g / L, spray and dehydrate it at 230°C to obtain hydrated magnesium chloride, and then add it to a fluidized bed pyrolysis furnace for pyrolysis. The temperature is 400°C, the pyrolysis time is 2 hours, and the magnesium oxide solid and hydrogen chloride gas are obtained. The purity of magnesium oxide is 87%. After the hydrogen chloride gas is dedusted by a cyclone, it is absorbed by circulating water to produce 30% hydrochloric acid, and returns to the rare earth ore acid dissolution process.
[0065] Magnesium oxide solids are prepared by pulping and carbonization to obtain pure magnesium bicarbonate solution with a concentration of 6.5g / L. The magnesium bicarbonate solution is pretreated with 1.35mol / L P507 organic phase in comparison with O / A=0.67:1 to obtain a solution containing Magnesium-loaded organic, the...
PUM
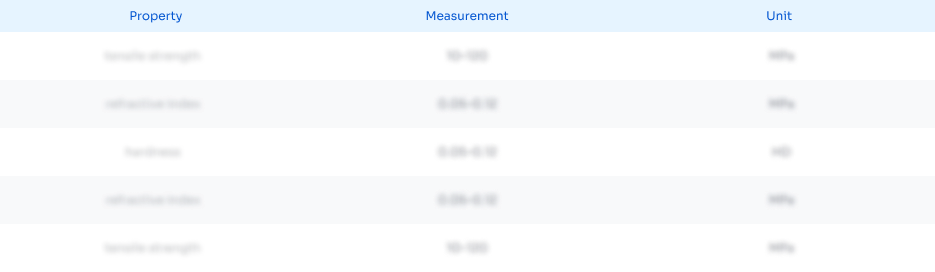
Abstract
Description
Claims
Application Information

- Generate Ideas
- Intellectual Property
- Life Sciences
- Materials
- Tech Scout
- Unparalleled Data Quality
- Higher Quality Content
- 60% Fewer Hallucinations
Browse by: Latest US Patents, China's latest patents, Technical Efficacy Thesaurus, Application Domain, Technology Topic, Popular Technical Reports.
© 2025 PatSnap. All rights reserved.Legal|Privacy policy|Modern Slavery Act Transparency Statement|Sitemap|About US| Contact US: help@patsnap.com