Submerged-arc welding flux matched with 850MPa-grade weather-proof high-strength steel
A technology of 850mpa, high-strength steel, applied in the field of submerged arc welding flux for 850MPa-grade weather-resistant high-strength steel, can solve the problems of embrittlement in the coarse-grained region, poor working conditions, poor low temperature toughness, etc., and achieves low crystal water content and good technology performance, good plasticity and toughness
- Summary
- Abstract
- Description
- Claims
- Application Information
AI Technical Summary
Problems solved by technology
Method used
Image
Examples
Embodiment 1
[0041] According to the component content of Example 1 in the above table 1, put each raw material in the mixer, stir and mix evenly, add 20% water glass and stir and mix, so that various powdery raw materials are mixed to form granules, granulated, and then Baking at a low temperature of 200°C, sintering at a high temperature of 700°C, and sieving to obtain flux No. 1 with an alkalinity of 3.0.
Embodiment 2
[0043] According to the component content of Example 2 in Table 1 above, put each raw material in a mixer, stir and mix evenly, add 21% sodium water glass and mix, granulate, and bake the obtained granules at a low temperature of 230°C, Sintered at 730°C and sieved to obtain flux No. 1 with an alkalinity of 2.9.
Embodiment 3
[0045] According to the component content of Example 3 in Table 1 above, put each raw material in a mixer, stir and mix evenly, add 21.5% sodium water glass to mix and granulate, then bake at 220°C at low temperature, and sinter at 680°C at high temperature , sieve to obtain the No. 3 flux with an alkalinity of 3.0.
PUM
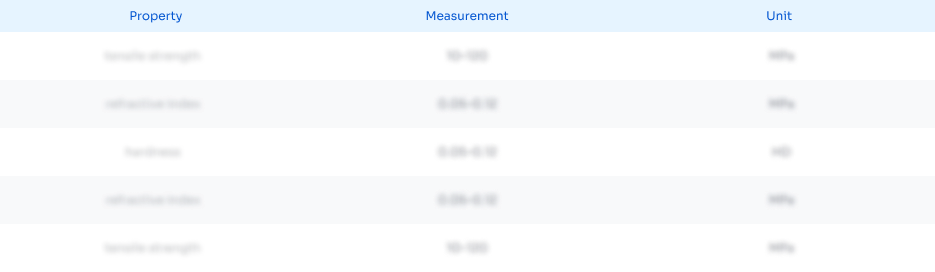
Abstract
Description
Claims
Application Information

- Generate Ideas
- Intellectual Property
- Life Sciences
- Materials
- Tech Scout
- Unparalleled Data Quality
- Higher Quality Content
- 60% Fewer Hallucinations
Browse by: Latest US Patents, China's latest patents, Technical Efficacy Thesaurus, Application Domain, Technology Topic, Popular Technical Reports.
© 2025 PatSnap. All rights reserved.Legal|Privacy policy|Modern Slavery Act Transparency Statement|Sitemap|About US| Contact US: help@patsnap.com