Double-drum settling denitration chamber jet lower gas inlet fuel gas and fuel oil corner tube boiler
A corner tube boiler and double drum technology, which is applied to water tube steam boilers, boiler water tubes, steam boilers, etc., can solve the problems of high concentration of nitrogen oxides, boilers that cannot meet the emission requirements, and pollute the environment, so as to reduce emissions, Simple structure and effect of improving thermal efficiency
- Summary
- Abstract
- Description
- Claims
- Application Information
AI Technical Summary
Problems solved by technology
Method used
Image
Examples
Embodiment 1
[0022] The invention provides a double-drum subsidence denitrification chamber injection gas-fired corner-tube boiler, such as figure 1 As shown, it includes the boiler body part and the combustion system part. The furnace body part of the boiler includes a boiler body 1, and six front side support downpipes 15, a first throttling ring 4, a middle support downpipe 20, a second throttling ring 34, The rear side supports the downcomer 27, the third throttle ring 35, the upper drum 23 and the lower drum 31 arranged on the upper right part of the boiler body 1, the convection tube bundle 28 between the upper drum and the lower drum, and the upper drum 23 Connected water inlet pipe 22 and outlet pipe 21, front downpipe 26, side downpipe 24, rear downpipe 25, upper return pipe 18, side water wall 5, side water wall lower header 10, side water wall upper header 2. The upper part of the furnace 3, the lower part of the oblique lower intake furnace 7, the front arch water wall 6, the ...
Embodiment 2
[0030] This embodiment is a further improvement made on the basis of Embodiment 1, including all the technical features of Embodiment 1, such as figure 2 As shown, a superheater is installed on the upper part of the upper sedimentation denitrification chamber.
[0031] The working process and principle of the present invention are as follows: firstly, fuel gas is injected into the furnace 7 and 3 through the gas (fuel) inlet 8 through the oblique burner 11 for combustion, and the heat generated is absorbed by the front arch water wall 6 of the furnace and the rear arch water wall 6. The arched water wall 13 is absorbed by the side water wall 5, and the cooled flue gas passes through the upper sedimentation denitrification chamber 19, descends, enters the lower sedimentation denitrification chamber 29, ascends, enters the convection tube bundle 28 for flushing and heat exchange, and completes the entire heat exchange process. The flue gas outlet 30 is discharged to complete th...
PUM
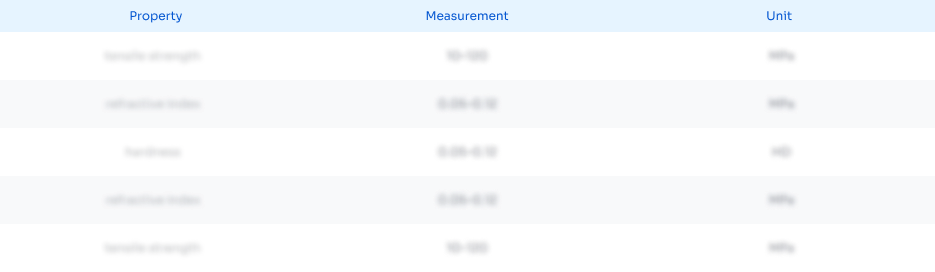
Abstract
Description
Claims
Application Information

- Generate Ideas
- Intellectual Property
- Life Sciences
- Materials
- Tech Scout
- Unparalleled Data Quality
- Higher Quality Content
- 60% Fewer Hallucinations
Browse by: Latest US Patents, China's latest patents, Technical Efficacy Thesaurus, Application Domain, Technology Topic, Popular Technical Reports.
© 2025 PatSnap. All rights reserved.Legal|Privacy policy|Modern Slavery Act Transparency Statement|Sitemap|About US| Contact US: help@patsnap.com