Method for performing surface modification on reinforcing fiber by using crystalline polyaryletherketone sizing agent
A polyaryletherketone and reinforced fiber technology, which is applied in the direction of carbon fiber, fiber treatment, fiber type, etc., can solve the problems of powder and fiber bundles not having adhesive force, PEEK melt viscosity is high, and thermal decomposition temperature is low, etc., to achieve Meet the needs of different composite materials, mild post-treatment means, and the effect of a large molecular weight range
- Summary
- Abstract
- Description
- Claims
- Application Information
AI Technical Summary
Problems solved by technology
Method used
Image
Examples
Embodiment 1
[0040] Dissolve 2.5g of ketimine polyetheretherketone (number-average molecular weight: 2000g / mol) in 997.5mL of NMP, and place it in a sizing tank with an effective stroke of 1m after it is completely dissolved. The carbon fiber bundles are subjected to sizing treatment; the carbon fibers after preliminary sizing are dried in NMP at 230°C in a resistance wire evaporator; the fiber bundles from which the solvent has been removed are introduced into a hydrolysis tank with 0.1mol / L dilute sulfuric acid for acidification treatment for 2 hours, and obtained after hydrolysis Carbon fiber bundles sized with crystalline polyether ether ketone, the carbon fiber bundles are dried at 150° C. and then wound up to obtain carbon fibers sized with crystalline polyether ether ketone. The surface morphology of carbon fiber before and after sizing is as follows: figure 1 As shown, its IFSS with PEEK is 60MPa, which is 100% higher than that of unsized carbon fiber (30MPa) (IFSS test curve see ...
Embodiment 2
[0042] Dissolve 10g of ketimine polyetheretherketoneketone (number-average molecular weight 4000g / mol) in 1040mL of DMF, slowly add 0.25g of carbon nanotubes under ultrasonic vibration conditions after complete dissolution, and place them in an effective stroke of 10mm after fully dispersed In the sizing tank, sizing treatment is performed on the carbon fiber bundles that have been washed off the sizing agent (the method of removing the sizing agent is ultrasonic washing with acetone for 48 hours) at a rate of 1 mm / min; the carbon fibers after preliminary sizing are heated in a resistance wire evaporator at 200 ° C Dry the DMF; the fiber bundles from which the solvent has been removed are introduced into a hydrolysis tank equipped with 0.9mol / L dilute sulfuric acid for acidification treatment for 2 hours, and after hydrolysis, crystalline polyetheretherketoneketone sized carbon fiber bundles are obtained. Winding after drying to obtain crystalline polyether ether ketone sized c...
Embodiment 3
[0044] Dissolve 10g of ketimine polyetherketone (number-average molecular weight 6000g / mol) in 1060mL of DMF, slowly add 0.5g of acidified carbon nanotubes under ultrasonic conditions after it is completely dissolved, and place it in a sizing machine with an effective stroke of 1m In the tank, the unsized basalt fiber was sized at a rate of 100 mm / min; the basalt fiber after preliminary sizing was dried in an infrared heating evaporator at 210 ° C; Acidification treatment in a hydrolysis tank with L dilute hydrochloric acid for 2 hours, after hydrolysis, basalt fiber bundles sized with crystalline polyetherketone were obtained, and the basalt fiber bundles were dried at 150°C and rolled up to obtain basalt fibers sized with crystalline polyetherketone . Its IFSS with PEEK is 78MPa, a 160% increase compared to unsized basalt fiber (31MPa).
PUM
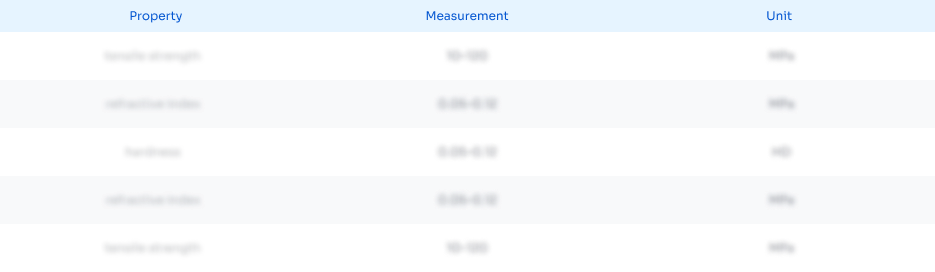
Abstract
Description
Claims
Application Information

- R&D
- Intellectual Property
- Life Sciences
- Materials
- Tech Scout
- Unparalleled Data Quality
- Higher Quality Content
- 60% Fewer Hallucinations
Browse by: Latest US Patents, China's latest patents, Technical Efficacy Thesaurus, Application Domain, Technology Topic, Popular Technical Reports.
© 2025 PatSnap. All rights reserved.Legal|Privacy policy|Modern Slavery Act Transparency Statement|Sitemap|About US| Contact US: help@patsnap.com