Sintering flue gas synergistic treatment system
A technology of sintering flue gas and flue gas condensation, which is applied in the direction of gas treatment, climate sustainability, and combustion technology mitigation. It can solve the problems of poor system operation stability, low utilization rate of by-products, equipment corrosion, etc., and reduce operating costs. , Long-term stable operation with low energy consumption and small footprint
- Summary
- Abstract
- Description
- Claims
- Application Information
AI Technical Summary
Problems solved by technology
Method used
Image
Examples
Embodiment
[0027] Embodiment: A kind of sintering flue gas collaborative management system, such as Figure 1-Figure 8 As shown, it includes an electrostatic precipitator 1, a first blower fan 2, a desulfurization device 3, a flue gas condensation dehydrator 4, a flue gas preheater 5, a denitrification device 6, a bag filter 7, a pipeline 8, and a chimney 10 connected to the second blower 9, the electrostatic precipitator 1, the first blower 2, the desulfurization equipment 3, the flue gas condensation water remover 4, the flue gas pre-heater 5, the denitrification equipment 6, the bag filter 7, the second The fan 9 and the chimney 10 are arranged in sequence along the sintering flue gas treatment process, the input end of the electric precipitator 1 is used to feed the sintering flue gas, and the output end of the electric precipitator 1 is input through the pipeline 8 and the first fan 2 The output end of the first fan 2 is connected to the input end of the desulfurization equipment 3 ...
PUM
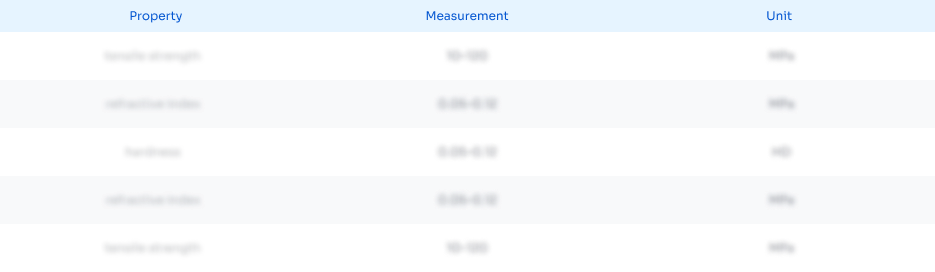
Abstract
Description
Claims
Application Information

- R&D
- Intellectual Property
- Life Sciences
- Materials
- Tech Scout
- Unparalleled Data Quality
- Higher Quality Content
- 60% Fewer Hallucinations
Browse by: Latest US Patents, China's latest patents, Technical Efficacy Thesaurus, Application Domain, Technology Topic, Popular Technical Reports.
© 2025 PatSnap. All rights reserved.Legal|Privacy policy|Modern Slavery Act Transparency Statement|Sitemap|About US| Contact US: help@patsnap.com