Method for preparing bismaleimide resin-based composite material by chemical vapor deposition method, and application of composite material
A bismaleimide resin, chemical vapor deposition technology, used in textiles and papermaking, fiber processing, carbon fiber and other directions, can solve problems such as unattainable mechanical properties, achieve weak interface bonding strength, improve mechanical properties, The effect of improving impact performance
- Summary
- Abstract
- Description
- Claims
- Application Information
AI Technical Summary
Problems solved by technology
Method used
Image
Examples
Embodiment 1
[0034] This embodiment is a method for preparing a bismaleimide resin-based composite material by chemical vapor deposition using a carbon fiber-carbon nanotube micro-nano synergistic reinforcement phase, which is carried out according to the following steps:
[0035] (1) Carbon fiber surface treatment: Put the carbon fiber in excess acetone, heat and reflux at 60°C for 24 hours, rinse with acetone repeatedly, and then dry. The above carbon fibers were placed in excess concentrated nitric acid, reacted at a constant temperature of 60°C for 2 hours, washed with deionized water repeatedly and dried.
[0036] (2) Loading metal ions: place the surface-treated carbon fiber in 0.1mol / L NiNO 3 Soak in the aqueous solution for 1 hour, take out the carbon fiber and place it in an oven to dry the surface moisture, nickel nitrate particles will precipitate and crystallize on the surface of the carbon fiber.
[0037] (3) Carbon nanotube growth: place the carbon fiber treated in the previ...
Embodiment 2
[0045] This embodiment is a method for preparing a bismaleimide resin-based composite material by chemical vapor deposition using a carbon fiber-carbon nanotube micro-nano synergistic reinforcement phase, which is carried out according to the following steps:
[0046] (1) Carbon fiber surface treatment: Put the carbon fiber in excess acetone, heat and reflux at 60°C for 24 hours, rinse with acetone repeatedly, and then dry. The above carbon fibers were placed in excess concentrated nitric acid, reacted at a constant temperature of 60°C for 2 hours, washed with deionized water repeatedly and dried.
[0047] (2) Loading metal ions: place the surface-treated carbon fiber in 0.15mol / L NiNO 3 Soak in the aqueous solution for 1 hour, take out the carbon fiber and place it in an oven to dry the surface moisture, nickel nitrate particles will precipitate and crystallize on the surface of the carbon fiber.
[0048] (3) Carbon nanotube growth: place the carbon fiber treated in the prev...
Embodiment 3
[0055] This embodiment is a method for preparing a bismaleimide resin-based composite material by chemical vapor deposition using a carbon fiber-carbon nanotube micro-nano synergistic reinforcement phase, which is carried out according to the following steps:
[0056] (1) Carbon fiber surface treatment: put carbon fiber in excess acetone, heat and reflux at 65°C for 24 hours, rinse with acetone repeatedly, and then dry. The above carbon fibers were placed in excess concentrated nitric acid, reacted at a constant temperature of 65°C for 2 hours, washed with deionized water repeatedly and dried.
[0057] (2) Loading metal ions: place the surface-treated carbon fiber in 0.1mol / L NiNO 3 Soak in the aqueous solution for 1.5h, take out the carbon fiber and place it in an oven to dry the surface moisture, nickel nitrate particles will precipitate and crystallize on the surface of the carbon fiber.
[0058] (3) Carbon nanotube growth: place the carbon fiber treated in the previous tw...
PUM
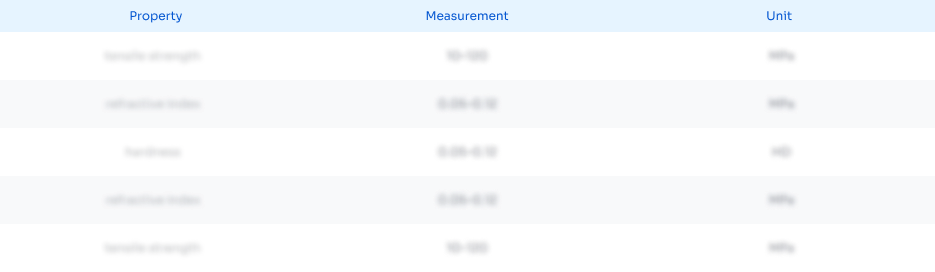
Abstract
Description
Claims
Application Information

- R&D
- Intellectual Property
- Life Sciences
- Materials
- Tech Scout
- Unparalleled Data Quality
- Higher Quality Content
- 60% Fewer Hallucinations
Browse by: Latest US Patents, China's latest patents, Technical Efficacy Thesaurus, Application Domain, Technology Topic, Popular Technical Reports.
© 2025 PatSnap. All rights reserved.Legal|Privacy policy|Modern Slavery Act Transparency Statement|Sitemap|About US| Contact US: help@patsnap.com