Aluminum pipe surface resin coating system
A resin coating, aluminum tube technology, applied to the device for coating liquid on the surface, pretreatment surface, coating and other directions, can solve the problems of equipment jitter, unsmooth feeding, and back and forth deviation of the entire line, and reduce the Risk of stretching, reducing risk of bending, reducing the effect of non-conforming products
- Summary
- Abstract
- Description
- Claims
- Application Information
AI Technical Summary
Problems solved by technology
Method used
Image
Examples
Embodiment Construction
[0041] The present invention will be described in detail below in conjunction with the accompanying drawings.
[0042] Such as figure 1The resin coating system on the surface of the aluminum tube is sequentially provided with a discharge unit 1 for outputting the aluminum tube 600, a cleaning unit 3 for cleaning the surface of the aluminum tube 600, and a drying unit for drying the aluminum tube 600 according to the traveling direction of the aluminum tube 600. Surface drying unit 4, glue coating unit 5 for coating glue on the surface of aluminum tube 600, heating unit 6 for heating aluminum tube 600, resin coating unit 8 for coating resin on the surface of aluminum tube 600, The cooling unit 9 for cooling the aluminum tube 600, the traction unit 10 for applying power to the aluminum tube 600 and the collection unit for collecting the aluminum tube 600 are arranged between the discharge unit 1 and the cleaning unit 3 for the aluminum The pipe diameter correction unit 2 for sh...
PUM
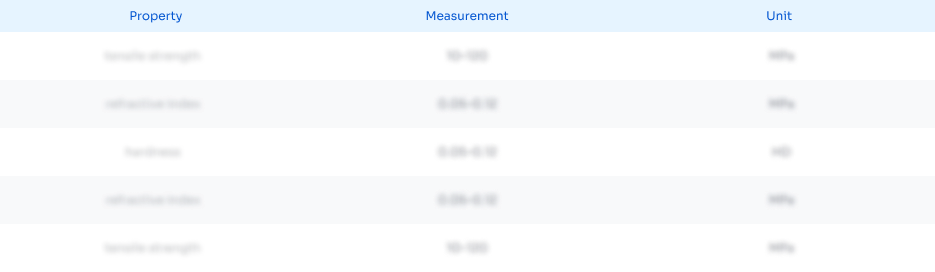
Abstract
Description
Claims
Application Information

- Generate Ideas
- Intellectual Property
- Life Sciences
- Materials
- Tech Scout
- Unparalleled Data Quality
- Higher Quality Content
- 60% Fewer Hallucinations
Browse by: Latest US Patents, China's latest patents, Technical Efficacy Thesaurus, Application Domain, Technology Topic, Popular Technical Reports.
© 2025 PatSnap. All rights reserved.Legal|Privacy policy|Modern Slavery Act Transparency Statement|Sitemap|About US| Contact US: help@patsnap.com