Non-quenched and tempered steel for automobile parts and production process thereof
A technology of auto parts and non-quenched and tempered steel, applied in the field of metallurgy, can solve problems such as poor purity of molten steel, poor microalloying technology, and unsatisfactory mechanical properties, and achieve optimal effect, uniform and refined material structure , the effect of grain refinement
- Summary
- Abstract
- Description
- Claims
- Application Information
AI Technical Summary
Problems solved by technology
Method used
Image
Examples
Embodiment 1
[0043] 120t converter process
[0044] 1. End point of converter: C content 0.12%, P content 0.009%, tapping temperature 1642°C.
[0045] 2. After 1 minute and 30 seconds of converter tapping, according to the residual alloy composition content, and after calculation, add the corresponding amount of ferroalloy, 700 kg of refining slag, and 450 kg of lime.
[0046] 3. After the converter is tapped, the molten steel is hoisted to the argon station, and then fed into the Al line for 380 meters at the argon station.
[0047] LF refining furnace process
[0048] 1200m of nitrogen-manganese wire is fed after LF, 50Kg of aluminum particles and 100Kg of SiC are used for diffusion deoxidation of steel slag during LF refining, the manganese content of LF furnace is controlled to 1.29% before tapping, and then aluminum wire is fed, ferro-titanium is added, and when LF is discharged Sampling and testing showed that the aluminum content in molten steel was 0.024%, the titanium content wa...
Embodiment 2
[0057] Converter process
[0058] 1. End point of converter: C content 0.13%, P content 0.008%, tapping temperature 1619℃. After the converter is tapped, the molten steel is hoisted to the argon station, and then 370 meters of Al wire is fed into the argon station, and the others are the same as in embodiment 1.
[0059] LF refining furnace process
[0060] Feed 1180m of nitrogen-manganese wire after entering LF, control the manganese content to 1.28% before tapping the LF furnace, then feed the aluminum wire, add ferro-titanium, and take samples for testing when the LF exits, the aluminum content in the molten steel is 0.023%, the titanium content is 0.022%, the sulfur Content 0.056%, other is with embodiment 1.
[0061] RH vacuum treatment process
[0062] The RH circulation time is 34min, of which the high vacuum (≤1.33mbar) time is 17min, the RH lifting gas uses nitrogen throughout the whole process, and the last 12min uses low vacuum (100Mpa), and feeds 260m of MnN wir...
Embodiment 3
[0068] Converter process
[0069] 1. End point of converter: C content 0.08%, P content 0.013%, tapping temperature 1633°C. After the converter is tapped, the molten steel is hoisted to the argon station, and then 400 meters of Al wire is fed into the argon station, and the others are the same as in embodiment 1.
[0070] LF refining furnace process
[0071] Feed 1240m of nitrogen-manganese wire after entering LF, control the manganese content of 1.31% before tapping the LF furnace, then feed the aluminum wire, add ferro-titanium, and take samples for testing when the LF exits, the aluminum content in the molten steel is 0.025%, the titanium content is 0.023%, the sulfur Content 0.053%, other is with embodiment 1.
[0072] RH vacuum treatment process
[0073] The RH circulation time is 34min30S, of which the high vacuum (≤1.33mbar) time is 17min, the RH lifting gas uses nitrogen throughout the whole process, and the last 12min uses low vacuum (100Mpa), and after the RH trea...
PUM
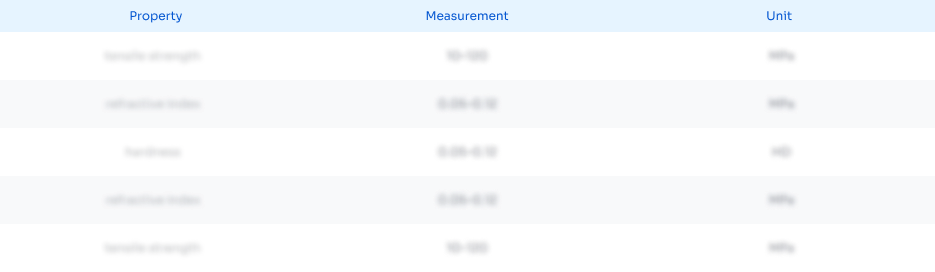
Abstract
Description
Claims
Application Information

- R&D
- Intellectual Property
- Life Sciences
- Materials
- Tech Scout
- Unparalleled Data Quality
- Higher Quality Content
- 60% Fewer Hallucinations
Browse by: Latest US Patents, China's latest patents, Technical Efficacy Thesaurus, Application Domain, Technology Topic, Popular Technical Reports.
© 2025 PatSnap. All rights reserved.Legal|Privacy policy|Modern Slavery Act Transparency Statement|Sitemap|About US| Contact US: help@patsnap.com