A method for recovering high-purity silicon and silicon carbide from crystalline silicon cutting waste
A technology for cutting waste and silicon carbide, which is applied in the direction of silicon carbide, chemical instruments and methods, carbide, etc., can solve the problems of unsatisfactory recovery of high-purity silicon, no industrialization reports, and difficult separation, so as to increase production rate and consumption Low, Enhanced Effects
- Summary
- Abstract
- Description
- Claims
- Application Information
AI Technical Summary
Problems solved by technology
Method used
Image
Examples
Embodiment 1
[0047] (1) Pretreatment of slurry
[0048] Mix 15g of crystalline silicon cutting waste with 150mL of absolute ethanol solution to form a suspension system, stir at room temperature and pressure for 2 hours, wash the obtained suspension with water and suction filter, and then filter and dry to obtain silicon and silicon carbide. dry mix;
[0049] (2) High temperature treatment
[0050] Place the dry mixture of silicon and silicon carbide obtained after pretreatment in a heating furnace, first vacuumize it, then pass in argon, raise the temperature to 500 ° C, keep the temperature for 1 hour, and then cool it to room temperature to obtain high temperature treated silicon and silicon carbide mixture;
[0051] (3) pickling treatment
[0052] Mix the high-temperature-treated silicon and silicon carbide mixture with 2mol / L sulfuric acid solution, control the reaction temperature at 60°C, and the reaction time for 4 hours. After the reaction is completed, filter, wash and dry the...
Embodiment 2
[0057] (1) Pretreatment of slurry
[0058] Mix 15g of crystalline silicon cutting waste with 200mL of acetone solution to form a suspension system, stir at room temperature and pressure for 3 hours, wash the obtained suspension with water and suction filter, then filter and dry to obtain a dry mixture of silicon and silicon carbide material;
[0059] (2) High temperature treatment
[0060] Place the dry mixture of silicon and silicon carbide obtained after pretreatment in a heating furnace, first vacuumize it, then pass in argon gas, raise the temperature to 450 ° C, keep the temperature for 1 hour, and then cool to room temperature to obtain high temperature treated silicon and silicon carbide mixture;
[0061] (3) pickling treatment
[0062] Mix the high-temperature-treated silicon and silicon carbide mixture with 2mol / L sulfuric acid solution, control the reaction temperature at 60°C, and the reaction time for 4 hours. After the reaction is completed, filter, wash and dr...
Embodiment 3
[0067] (1) Pretreatment of slurry
[0068] Mix 15g of crystalline silicon cutting waste with 150mL of absolute ethanol solution to form a suspension system, stir at room temperature and pressure for 2 hours, wash the obtained suspension with water and suction filter, and then filter and dry to obtain silicon and silicon carbide. dry mix;
[0069] (2) High temperature treatment
[0070] Put the dry mixture of silicon and silicon carbide obtained after pretreatment in a heating furnace, first vacuumize it, then pass in hydrogen gas, raise the temperature to 450 ° C, keep the temperature for 1 hour, and then cool to room temperature to obtain silicon and silicon carbide after high temperature treatment Silicon carbide mixture;
[0071] (3) pickling treatment
[0072] Mix the high-temperature-treated silicon and silicon carbide mixture with 1mol / L sulfuric acid solution, control the reaction temperature at 60°C, and the reaction time for 4 hours. After the reaction is completed...
PUM
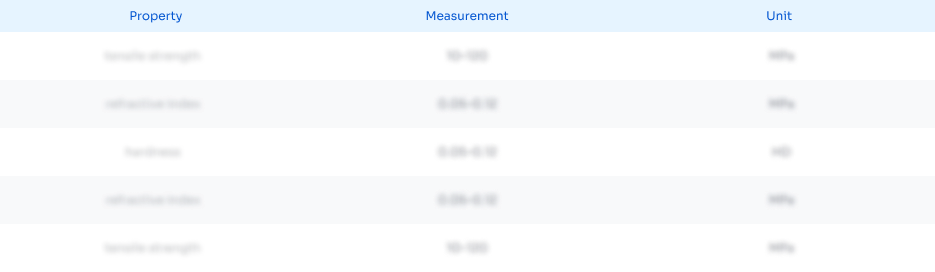
Abstract
Description
Claims
Application Information

- Generate Ideas
- Intellectual Property
- Life Sciences
- Materials
- Tech Scout
- Unparalleled Data Quality
- Higher Quality Content
- 60% Fewer Hallucinations
Browse by: Latest US Patents, China's latest patents, Technical Efficacy Thesaurus, Application Domain, Technology Topic, Popular Technical Reports.
© 2025 PatSnap. All rights reserved.Legal|Privacy policy|Modern Slavery Act Transparency Statement|Sitemap|About US| Contact US: help@patsnap.com