MEMS diaphragm and MEMS sensor chip
A technology of diaphragm and sensing part, which is applied in the field of MEMS diaphragm and MEMS sensor chip, can solve the problems of inability to accurately control film stress, low sensitivity of micro-electromechanical devices, sensitivity variation, etc., achieve good acoustic sensing performance, increase The effect of large capacitance value and increased effective area
- Summary
- Abstract
- Description
- Claims
- Application Information
AI Technical Summary
Problems solved by technology
Method used
Image
Examples
Embodiment Construction
[0030] Before describing the embodiments in detail, it should be understood that the present invention is not limited to the detailed structures or arrangements of components described herein below or in the accompanying drawings. The present invention can be implemented in other ways. Also, it should be understood that the phraseology and terminology used herein are for descriptive purposes only and should not be interpreted as limiting. The terms "including", "comprising", "having" and similar expressions used herein are meant to include the items listed thereafter, their equivalents and other additional items. In particular, when "a certain component" is described, the present invention does not limit the number of the component to one, and may also include multiples.
[0031] Such as figure 1 Shown is a schematic structural view of the MEMS diaphragm in an embodiment of the present invention. The MEMS diaphragm 10 is applied in microelectromechanical devices, for exampl...
PUM
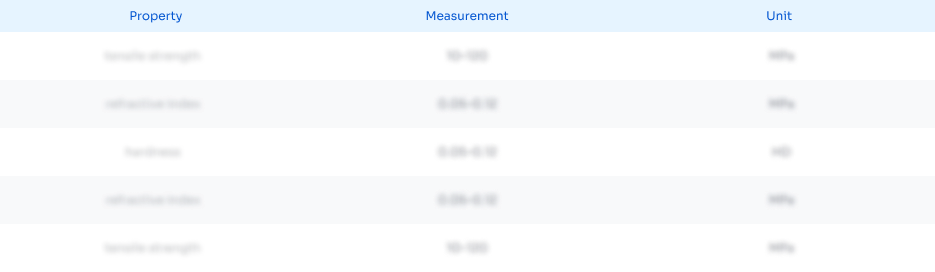
Abstract
Description
Claims
Application Information

- R&D Engineer
- R&D Manager
- IP Professional
- Industry Leading Data Capabilities
- Powerful AI technology
- Patent DNA Extraction
Browse by: Latest US Patents, China's latest patents, Technical Efficacy Thesaurus, Application Domain, Technology Topic, Popular Technical Reports.
© 2024 PatSnap. All rights reserved.Legal|Privacy policy|Modern Slavery Act Transparency Statement|Sitemap|About US| Contact US: help@patsnap.com