Method for purifying brine by using mixed liquid of ammonia alkali waste residues and waste liquids and flue gas
A technology for purification of ammonia-alkali waste slag and brine, which is applied in the fields of alkali metal halide purification, alkali metal chloride, energy input, etc., can solve problems such as unreasonable distribution of industrial layout, extended product transportation distance, etc., and improve brine recovery rate , reduce the content of sulfate ions, and reduce the effect of treatment costs
- Summary
- Abstract
- Description
- Claims
- Application Information
AI Technical Summary
Problems solved by technology
Method used
Image
Examples
Embodiment 1
[0040] S1. Separating the waste slag and waste liquid mixed liquid from the soda ash ammonia distillation process through the cyclone sand separator, and sieving out the alkali slag with a particle size greater than 1.2mm;
[0041] S2. After sand separation, the high-temperature waste residue and waste liquid mixture first enters the waste heat power generation process to cool down, then enters the flash barrel for vacuum flashing, and then cools down to below 68°C. After cooling, the waste residue and waste liquid mixture enters the mixing machine with a stirring device Temporary storage of liquid storage tanks;
[0042] S3. Transport the mixed liquid of waste slag and waste liquid in the above S2 to the storage tank of the mine through two pipelines by a slurry pump for temporary storage, and continuously and fully stir;
[0043] Wherein the pipeline is a corrosion-resistant, abrasion-resistant, temperature-resistant, smooth non-metallic pipeline.
[0044] Wherein the transpo...
Embodiment 2
[0050] S1. Separating the waste slag and waste liquid mixed liquid from the soda ash ammonia distillation process through the cyclone sand separator, and sieving out the alkali slag with a particle size greater than 1.2mm;
[0051] S2. After sand separation, the high-temperature waste slag and waste liquid mixture first enters the waste heat power generation process to cool down, then enters the flash tank for vacuum flashing, and then cools down to below 68°C. After cooling, the waste slag and waste liquid mixture enters the mixing machine with a stirring device Temporary storage of liquid storage tanks;
[0052] S3. Transport the mixed liquid of waste slag and waste liquid in the above S2 to the storage tank of the mine through two pipelines by a slurry pump for temporary storage, and continuously and fully stir;
[0053] Wherein the pipeline is a corrosion-resistant, abrasion-resistant, temperature-resistant, smooth non-metallic pipeline.
[0054] Wherein the transportatio...
Embodiment 3
[0060] S1. Separating the waste slag and waste liquid mixed liquid from the soda ash ammonia distillation process through the cyclone sand separator, and sieving out the alkali slag with a particle size greater than 1.2mm;
[0061] S2. After sand separation, the high-temperature waste slag and waste liquid mixture first enters the waste heat power generation process to cool down, then enters the flash tank for vacuum flashing, and then cools down to below 68°C. After cooling, the waste slag and waste liquid mixture enters the mixing machine with a stirring device Temporary storage of liquid storage tanks;
[0062] S3. Transport the mixed liquid of waste slag and waste liquid in the above S2 to the storage tank of the mine through two pipelines by a slurry pump for temporary storage, and continuously and fully stir;
[0063] Wherein the pipeline is a corrosion-resistant, abrasion-resistant, temperature-resistant, smooth non-metallic pipeline.
[0064] Wherein the transportatio...
PUM
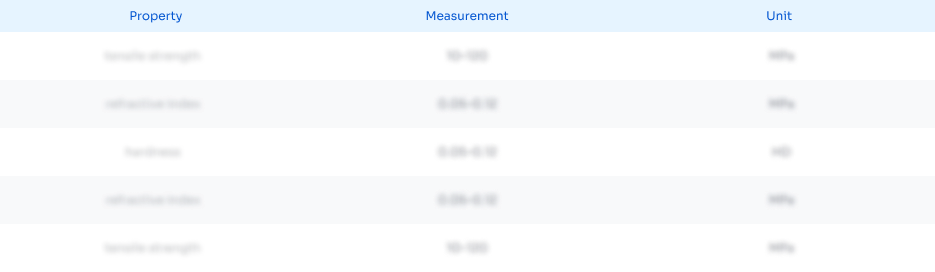
Abstract
Description
Claims
Application Information

- R&D
- Intellectual Property
- Life Sciences
- Materials
- Tech Scout
- Unparalleled Data Quality
- Higher Quality Content
- 60% Fewer Hallucinations
Browse by: Latest US Patents, China's latest patents, Technical Efficacy Thesaurus, Application Domain, Technology Topic, Popular Technical Reports.
© 2025 PatSnap. All rights reserved.Legal|Privacy policy|Modern Slavery Act Transparency Statement|Sitemap|About US| Contact US: help@patsnap.com