Welding method of composite steel plates
A welding method and technology for clad steel plates, applied in welding equipment, welding/welding/cutting items, arc welding equipment, etc., can solve the problems of a small number of high-tech welders, low welding efficiency of pure manual welding, and welding seam failure, etc. The effect of reducing the formation of harmful tissues, avoiding the formation of harmful tissues, preventing diffusion and aggregation
- Summary
- Abstract
- Description
- Claims
- Application Information
AI Technical Summary
Problems solved by technology
Method used
Image
Examples
Embodiment Construction
[0021] Taking the 4mm316L+18mmQ345R composite board as an example, the welding of the composite board weld seam includes the following steps:
[0022] 1. Use a plasma cutting machine to process the composite panel into a symmetrical X-shaped bevel, the bevel angle is 60±1°, the bevel gap is 2mm, and the blunt edge size is 4mm.
[0023] 2. The bottoming weld of the base material on the composite material side is manually welded with J507 electrode, and the electrode is baked at 350°C for 2 hours before welding. The welding current is 250A-400A, the welding voltage is 28-32V, and the welding speed is 300-450mm / Min , The dry elongation is 15-25mm. After the primer is completed, knock off the coating, and use an angle grinder to polish the weld to be smooth and smooth.
[0024] 3. The base material filling seam (4) on the composite material side is welded by submerged arc automatic welding. The welding material is H08A welding wire. The welding current is 350A-500A, the welding vo...
PUM
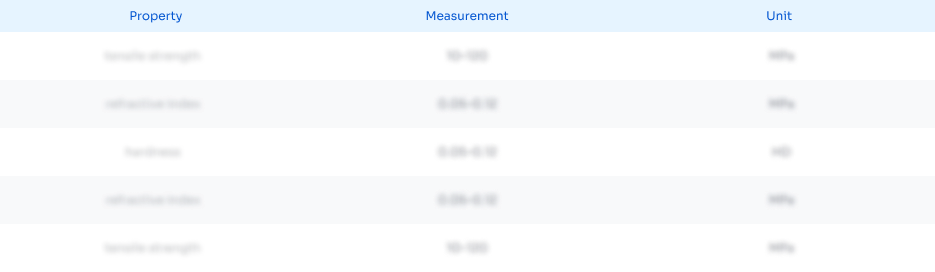
Abstract
Description
Claims
Application Information

- R&D
- Intellectual Property
- Life Sciences
- Materials
- Tech Scout
- Unparalleled Data Quality
- Higher Quality Content
- 60% Fewer Hallucinations
Browse by: Latest US Patents, China's latest patents, Technical Efficacy Thesaurus, Application Domain, Technology Topic, Popular Technical Reports.
© 2025 PatSnap. All rights reserved.Legal|Privacy policy|Modern Slavery Act Transparency Statement|Sitemap|About US| Contact US: help@patsnap.com