Ultra-clean treatment system and ultra-clean treatment method for VOCs in coking plant chemical industry product recovery area
A treatment system and treatment method technology, which is applied in the field of VOCs ultra-clean treatment system in the chemical production recovery area of coking plants, can solve the problems of complex process flow, small scope of application, high investment cost, etc., and achieve simple process flow and no secondary pollution , the effect of low investment
- Summary
- Abstract
- Description
- Claims
- Application Information
AI Technical Summary
Problems solved by technology
Method used
Image
Examples
Embodiment Construction
[0079] In order to illustrate the present invention more clearly, the present invention will be further described below in conjunction with preferred embodiments. Those skilled in the art should understand that the content specifically described below is illustrative rather than restrictive, and should not limit the protection scope of the present invention.
[0080] The present invention provides a preferred embodiment, such as figure 1 As shown, a VOCs ultra-clean treatment system in the chemical production recovery area of a coking plant includes sequentially connected: buffer tank 1, first gas-liquid heat exchanger 2, combustion furnace 3, second gas-liquid heat exchanger 4, desulfurization device, Bag filter 7, induced draft fan 8 and chimney 9.
[0081] The desulfurization device includes a desulfurizer nozzle 5 , a desulfurizer storage bin 10 , a manual slide valve 11 , a star feed valve 12 , a conveying fan 13 and a swirl rectifier 6 .
[0082] The desulfurizing ag...
PUM
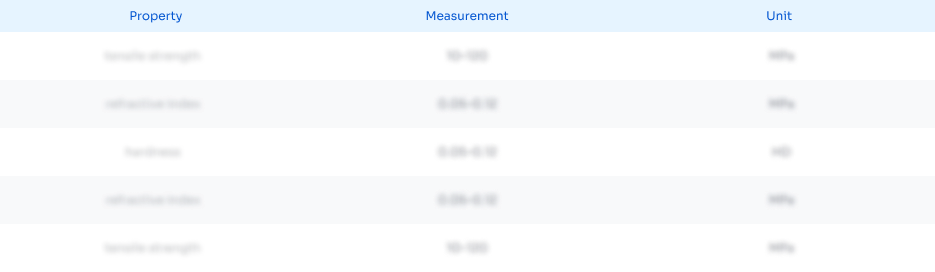
Abstract
Description
Claims
Application Information

- Generate Ideas
- Intellectual Property
- Life Sciences
- Materials
- Tech Scout
- Unparalleled Data Quality
- Higher Quality Content
- 60% Fewer Hallucinations
Browse by: Latest US Patents, China's latest patents, Technical Efficacy Thesaurus, Application Domain, Technology Topic, Popular Technical Reports.
© 2025 PatSnap. All rights reserved.Legal|Privacy policy|Modern Slavery Act Transparency Statement|Sitemap|About US| Contact US: help@patsnap.com