Method for preparing carbon nanotube reinforcing composite clad layers on surfaces of titanium alloys
A carbon nanotube, enhanced composite technology, applied in the direction of metal material coating process, coating, etc., can solve the problems of complex method and high cost, and achieve the effect of simple operation method, low cost, and improved tolerance.
- Summary
- Abstract
- Description
- Claims
- Application Information
AI Technical Summary
Problems solved by technology
Method used
Image
Examples
Embodiment 1
[0046] A surface modification method of titanium alloy using carbon nanotubes includes the following steps:
[0047] S1. Dispersion treatment of carbon nanotubes: first, prepare a 10g / L carboxymethyl cellulose aqueous solution, and then gradually add carbon nanotubes under the agitation of a magnetic stirrer until the concentration is 10g / L, and stir well. Disperse by ultrasonic vibration for 1 h to obtain a carbon nanotube solution.
[0048] S2. The configuration of the cladding material: add nickel-based self-fluxing alloy powder with a distribution size of 40μm-100μm into the dispersion of carbon nanotubes, the mass ratio of carbon nanotubes to nickel-based alloy powder is 1:20, and magnetically stirred The mixing is uniform, and the carbon nanotubes are fully coated on the surface of the nickel-based alloy powder. After the mixing is uniform, it is taken out and dried at 55°C.
[0049] S3. Immerse the polished TC4 titanium alloy into the carbon nanotube solution uniformly disper...
Embodiment 2
[0054] A surface modification method of titanium alloy using carbon nanotubes includes the following steps:
[0055] S1. Dispersion treatment of carbon nanotubes: first, prepare 15g / L carboxymethyl cellulose aqueous solution, and then gradually add carbon nanotubes under the agitation action of a magnetic stirrer until the concentration is 20g / L, and stir well. Disperse by ultrasonic vibration for 1 h to obtain a carbon nanotube solution.
[0056] S2. The configuration of the cladding material: add nickel-based self-fluxing alloy powder with a distribution size of 40μm-100μm into the dispersion of carbon nanotubes, the mass ratio of carbon nanotubes to nickel-based alloy powder is 1:20, and magnetically stirred The device is evenly mixed, and the carbon nanotubes are fully coated on the surface of the nickel-based alloy powder. After the mixture is evenly mixed, it is taken out and dried at 55°C;
[0057] S3. Immerse the polished TC4 titanium alloy into the carbon nanotube solution ...
Embodiment 3
[0062] A surface modification method of titanium alloy using carbon nanotubes includes the following steps:
[0063] S1. Dispersion treatment of carbon nanotubes: first configure 10g / L carboxymethyl cellulose organic dispersant, and then gradually add carbon nanotubes under the agitation of a magnetic stirrer until the concentration is 10g / L, and stir well. Then use ultrasonic vibration to disperse for 1 hour.
[0064] S2. The configuration of the cladding material: add nickel-based self-fluxing alloy powder with a distribution size of 40μm-100μm into the dispersion of carbon nanotubes, the mass ratio of carbon nanotubes to nickel-based alloy powder is 1:20, and magnetically stirred The mixing is uniform, and the carbon nanotubes are fully coated on the surface of the nickel-based alloy powder. After the mixing is uniform, it is taken out and dried at 55°C.
[0065] S3. Laser cladding: such as figure 1 As shown, under the protection of 15L / min argon gas, the powder in step S2 is tra...
PUM
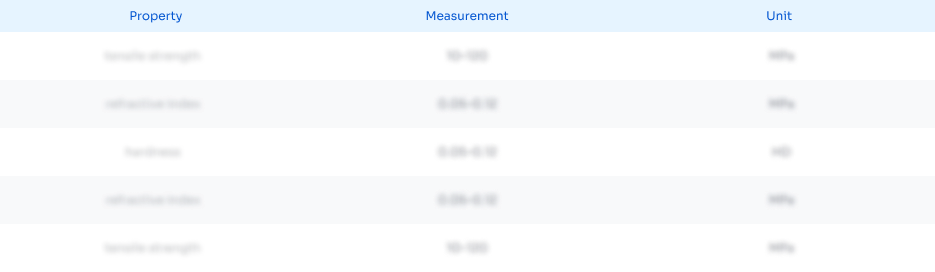
Abstract
Description
Claims
Application Information

- R&D
- Intellectual Property
- Life Sciences
- Materials
- Tech Scout
- Unparalleled Data Quality
- Higher Quality Content
- 60% Fewer Hallucinations
Browse by: Latest US Patents, China's latest patents, Technical Efficacy Thesaurus, Application Domain, Technology Topic, Popular Technical Reports.
© 2025 PatSnap. All rights reserved.Legal|Privacy policy|Modern Slavery Act Transparency Statement|Sitemap|About US| Contact US: help@patsnap.com