Special soldering tin paste used for welding multi-stage package patch element
A technology for chip components and solder paste, which is applied in welding media, welding equipment, welding/cutting media/materials, etc., can solve the problems of high temperature of printed circuit boards, reduced product performance, and high production costs, and achieves a wide range of applications. , The effect of low preparation cost and high service temperature
- Summary
- Abstract
- Description
- Claims
- Application Information
AI Technical Summary
Problems solved by technology
Method used
Examples
Embodiment 1
[0036] Take 30 grams of tin metal material and 70 grams of silver metal material, and put them into the intermediate frequency furnace through the feeding port. The temperature of the intermediate frequency furnace is set at 1100-1200 °C. Stainless steel container, cooled for later use;
[0037] Pour the master alloy obtained in the above steps into a stainless steel container and fully mix it with 1000 grams of tin powder at a temperature of 200-300 ° C, stir for 60 minutes, and then let it stand for 180 minutes to make an alloy for later use;
[0038]When the temperature drops to 150-180°C, add potassium metal powder with a mass percentage of 8 grams to the alloy prepared above, stir for 60 minutes, raise the temperature to 200-300°C, let it stand for 20 minutes, scoop out and cool , made into an alloy for use;
[0039] The above alloy is prepared into tin alloy powder through powder atomization forming equipment through classification and screening;
[0040] Take again, 2...
Embodiment 2
[0045] Take 10 grams of tin metal material and 100 grams of copper metal material, and put them into the intermediate frequency furnace through the feed port. The temperature of the intermediate frequency furnace is set at 1100-1200 °C. Stainless steel container, cooled for later use;
[0046] Pour the master alloy obtained in the above steps into a stainless steel container and fully mix it with 1000 grams of tin powder at a temperature of 200-300 ° C, stir for 60 minutes, and then let it stand for 180 minutes to make an alloy for later use;
[0047] When the temperature drops to 150-180°C, add 9 grams of potassium to the alloy prepared above, stir for 60 minutes, raise the temperature to 200-300°C, let stand for 20 minutes, scoop out and cool, and make Alloy for use;
[0048] The above alloy is prepared into tin alloy powder through powder atomization forming equipment through classification and screening;
[0049] Take again, 0.25 grams of copper and 0.4 grams of silver a...
Embodiment 3
[0054] Take 10 grams of tin metal material and 100 grams of antimony metal material, and put them into the intermediate frequency furnace through the feed port. The temperature of the intermediate frequency furnace is set at 650-800 °C. Stainless steel container, cooled for later use;
[0055] Take 63 grams of tin metal material and 37 grams of lead metal material, and put them into the intermediate frequency furnace through the feed port. The temperature of the intermediate frequency furnace is set at 1300-1400 °C. Stainless steel container, cooled for later use;
[0056] Pour the master alloy obtained in the above steps into a stainless steel container and fully mix it with 1000 grams of tin powder at a temperature of 200-300 ° C, stir for 60 minutes, and then let it stand for 180 minutes to make an alloy for later use;
[0057] When the temperature drops to 150-180°C, add 12 grams of potassium metal powder to the alloy prepared above, stir for 60 minutes, raise the tempera...
PUM
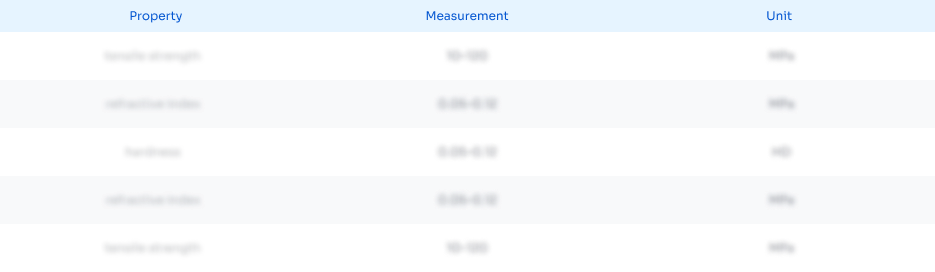
Abstract
Description
Claims
Application Information

- Generate Ideas
- Intellectual Property
- Life Sciences
- Materials
- Tech Scout
- Unparalleled Data Quality
- Higher Quality Content
- 60% Fewer Hallucinations
Browse by: Latest US Patents, China's latest patents, Technical Efficacy Thesaurus, Application Domain, Technology Topic, Popular Technical Reports.
© 2025 PatSnap. All rights reserved.Legal|Privacy policy|Modern Slavery Act Transparency Statement|Sitemap|About US| Contact US: help@patsnap.com