Method for separating and recovering electrolyte in waste power lithium batteries by means of ultrasonic enhanced extraction
An ultrasonic enhancement, separation and recovery technology, applied in separation methods, chemical instruments and methods, solvent extraction, etc., can solve the problems of secondary pollution and fluorine-containing wastewater, and achieve zero discharge of three wastes, high-efficiency separation, and a wide range of applications. Effect
- Summary
- Abstract
- Description
- Claims
- Application Information
AI Technical Summary
Problems solved by technology
Method used
Image
Examples
Embodiment 1
[0016] (1) Steps of electrified crushing of waste batteries under the protection of inert gas and closed atmosphere: 10kg of waste power ternary lithium batteries are charged and crushed under the protection of carbon dioxide gas and closed atmosphere. Crushed to obtain waste battery scraps, the size of scraps is 20mm*20mm. The crushed battery scraps are transported to the ultrasonic enhanced extraction process in a closed system.
[0017] (2) Steps of ultrasonically enhanced extraction and recovery of electrolyte in waste battery scraps: crushed battery scraps enter the ultrasonically enhanced extraction process, extraction temperature is 25°C, extraction time: 5min, extraction flow ratio: 1:5, so that the battery scraps The electrolyte in the material is extracted into the main extractant and auxiliary extractant, and at the same time, the electrode powder is completely separated from the copper and aluminum foil.
[0018] (3) Steps of organic solvent evaporation, condensat...
Embodiment 2
[0021] (1) Steps of electrified crushing of waste batteries under inert gas protection and closed atmosphere: 50kg of waste power lithium iron phosphate batteries are charged and crushed under nitrogen protection and closed atmosphere. Crushed to obtain waste battery scraps, the size of scraps is 20mm*20mm. The crushed battery scraps are transported to the ultrasonic enhanced extraction process in a closed system.
[0022] (2) Steps of ultrasonically enhanced extraction and recovery of electrolyte in waste battery scraps: crushed battery scraps enter the ultrasonically enhanced extraction process, extraction temperature is 20°C, extraction time: 60min, extraction flow ratio: 1:2. The electrolyte in the battery scrap is extracted into the main extractant and auxiliary extractant, and at the same time, the electrode powder is completely separated from the copper and aluminum foil.
[0023] (3) Steps of organic solvent evaporation, condensation, separation and recovery after ext...
Embodiment 3
[0025] (1) Steps of electrified crushing of waste batteries under inert gas protection and closed atmosphere: 200kg of waste power lithium cobalt oxide batteries are charged and crushed under argon protection and closed atmosphere. Crushed to obtain waste battery scraps, the size of scraps is 20mm*20mm. The crushed battery scraps are transported to the ultrasonic enhanced extraction process in a closed system.
[0026] (2) Steps of ultrasonically enhanced extraction and recovery of electrolyte in waste battery scrap: crushed battery scrap enters the ultrasonically enhanced extraction process, extraction temperature is 18°C, extraction time: 120min, extraction flow ratio: 1:1. The electrolyte in the battery scrap is extracted into the main extractant and auxiliary extractant, and at the same time, the electrode powder is completely separated from the copper and aluminum foil.
[0027] (3) Steps of organic solvent evaporation, condensation, separation and recovery after extract...
PUM
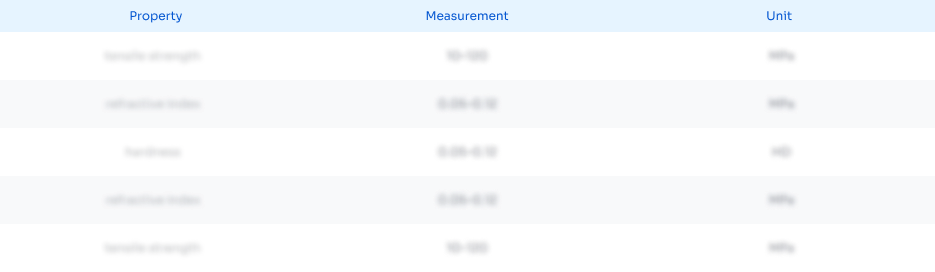
Abstract
Description
Claims
Application Information

- R&D Engineer
- R&D Manager
- IP Professional
- Industry Leading Data Capabilities
- Powerful AI technology
- Patent DNA Extraction
Browse by: Latest US Patents, China's latest patents, Technical Efficacy Thesaurus, Application Domain, Technology Topic, Popular Technical Reports.
© 2024 PatSnap. All rights reserved.Legal|Privacy policy|Modern Slavery Act Transparency Statement|Sitemap|About US| Contact US: help@patsnap.com