Calcined kaolin-based composite flame retardant for epoxy resin, and preparation and application of calcined kaolin-based composite flame retardant
A technology of composite flame retardant and calcined kaolin, which is applied in the field of flame retardant, can solve the problems of inability to withstand high temperature, difficulty in mixing uniformly, low decomposition temperature, etc., achieve tight and uniform combination, increase carbon residue, and improve flame retardant performance Effect
- Summary
- Abstract
- Description
- Claims
- Application Information
AI Technical Summary
Problems solved by technology
Method used
Image
Examples
Embodiment 1
[0031] According to the mass ratio of 1.8:1, take calcined kaolin and 85wt% phosphoric acid solution respectively, and then take powdered urea, the mass ratio of urea and phosphoric acid contained in phosphoric acid solution is 1:1; add calcined kaolin and phosphoric acid solution with In a three-necked flask with a reflux condenser and an electric stirrer, slowly heat to 75°C under mechanical stirring, and keep warm for 5 hours to obtain a mixture S1; add urea to the mixture S1 and stir thoroughly until the urea is completely dissolved to obtain a uniform mixture S2; Heat the mixture S2 to 100°C at a heating rate of 1°C / min. After the mixture S2 becomes thick and viscous, stop heating and keep it warm for 5 minutes to obtain the product; put the product in a vacuum oven, cure it at 180°C for 5 hours, and take it out. Cool to room temperature and grind to obtain a calcined kaolin-based composite flame retardant for epoxy resin.
Embodiment 2
[0034] According to the mass ratio of 1.8:1, take calcined kaolin and 85wt% phosphoric acid solution respectively, and then take powdered urea, the mass ratio of urea and phosphoric acid contained in phosphoric acid solution is 1:1; add calcined kaolin and phosphoric acid solution with In a three-necked flask with a reflux condenser and an electric stirrer, slowly heat to 95°C under mechanical stirring, and keep warm for 0.5h to obtain a mixture S1; add urea to the mixture S1, and stir well until the urea is completely dissolved to obtain a uniform mixture S2; Heat the mixture S2 to 150°C at a heating rate of 5°C / min. After the mixture S2 becomes thick and viscous, stop heating and keep it warm for 10 minutes to obtain the product; put the product in a vacuum oven and cure it at 250°C for 1 hour, and take it out , cooled to room temperature, and ground to obtain a calcined kaolin-based composite flame retardant for epoxy resin.
Embodiment 3
[0037] According to the mass ratio of 1.8:1, take calcined kaolin and 85wt% phosphoric acid solution respectively, and then take powdered urea, the mass ratio of urea and phosphoric acid contained in phosphoric acid solution is 1:1; add calcined kaolin and phosphoric acid solution with In a three-necked flask with a reflux condenser and an electric stirrer, slowly heat to 85°C under mechanical stirring, and keep it warm for 2.7 hours to obtain a mixture S1; add urea to the mixture S1 and stir thoroughly until the urea is completely dissolved to obtain a uniform mixture S2; The temperature of the mixture S2 was raised to 125°C at a heating rate of 3°C / min. After the mixture S2 became thick and viscous, the heating was stopped and the product was kept for 7.5 minutes to obtain the product; the product was put into a vacuum oven and cured at 215°C for 3 hours. Take it out, cool to room temperature, and grind to prepare a calcined kaolin-based composite flame retardant for epoxy resi...
PUM
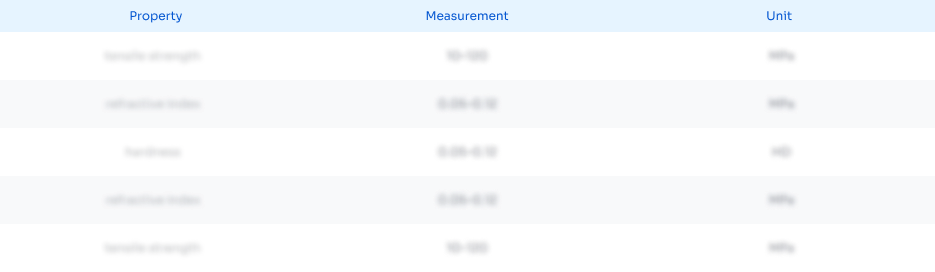
Abstract
Description
Claims
Application Information

- R&D
- Intellectual Property
- Life Sciences
- Materials
- Tech Scout
- Unparalleled Data Quality
- Higher Quality Content
- 60% Fewer Hallucinations
Browse by: Latest US Patents, China's latest patents, Technical Efficacy Thesaurus, Application Domain, Technology Topic, Popular Technical Reports.
© 2025 PatSnap. All rights reserved.Legal|Privacy policy|Modern Slavery Act Transparency Statement|Sitemap|About US| Contact US: help@patsnap.com