Method for preparing 2-oxo-2-furyl acetic acid by using continuous flow micro-channel reactor
A technology of microchannel reactor and channel reactor, which is applied in chemical instruments and methods, chemical/physical/physical chemical reactors, chemical/physical/physical chemical processes, etc., and can solve the problem of low yield and pollution discharge of "three wastes" Large and other problems, to achieve high purity, improve safety and environmental protection, and reduce costs
- Summary
- Abstract
- Description
- Claims
- Application Information
AI Technical Summary
Problems solved by technology
Method used
Image
Examples
Embodiment 1
[0036] 27.5g of 2-acetylfuran was dissolved in 150mL of 68% nitric acid to configure reaction solution 1, then 17.3g of sodium nitrite and 0.43g of toluenesulfonic acid (1% mol) were dissolved in 150mL of water, The molar ratio of the reaction solution 2, 2-acetylfuran and sodium nitrite is 1:1; the reaction solution 1 is poured into the cooling tower A, the reaction solution 2 is poured into the cooling tower B, and the temperature of the cooling tower is set to 5°C; after the pre-cooling is completed, use different metering pumps to pump the reaction solution 1 and the reaction solution 2 into the feed port of the continuous flow microchannel reactor, set the flow rate of the metering pump to be 5mL / min, and the microchannel reaction The temperature of the reactor is set at 60°C, and the pressure is about 1.55Mpa. After all the reaction liquid passes through the microchannel reactor, the product solution collected at the outlet is pumped into the extraction tower, and the ext...
Embodiment 2
[0038] 27.5g of 2-acetylfuran was dissolved in 150mL of 68% nitric acid to configure reaction solution 1, then 34.6g of sodium nitrite and 0.43g of toluenesulfonic acid (1% mol) were dissolved in 150mL of water, The molar ratio of the reaction solution 2, 2-acetylfuran and sodium nitrite is 1:2; the reaction solution 1 is poured into the cooling tower A, the reaction solution 2 is poured into the cooling tower B, and the temperature of the cooling tower is set to 5°C; after the pre-cooling is completed, use different metering pumps to pump the reaction solution 1 and reaction solution 2 into the feed port of the continuous flow microchannel reactor, set the flow rate of the metering pump to be 5mL / min, and the microchannel reaction The temperature of the reactor is set at 60°C, and the pressure is about 1.6Mpa. After all the reaction liquid passes through the microchannel reactor, the product solution collected at the outlet is pumped into the extraction tower, and the extracti...
Embodiment 3
[0040]27.5g of 2-acetylfuran was dissolved in 150mL of 68% nitric acid to configure reaction solution 1, then 51.9g of sodium nitrite and 0.43g of toluenesulfonic acid (1% mol) were dissolved in 150mL of water, Configure the reaction solution 2, the molar ratio of 2-acetylfuran and sodium nitrite is 1:3, pour the reaction solution 1 into the cooling tower A, and pour the reaction solution 2 into the cooling tower B, set the temperature of the cooling tower to 5 °C; after the pre-cooling is completed, use different metering pumps to pump the reaction solution 1 and reaction solution 2 into the feed port of the continuous flow microchannel reactor, set the flow rate of the metering pump to be 5mL / min, and the microchannel reactor The temperature is set at 60°C and the pressure is about 1.7Mpa. After all the reaction liquid passes through the microchannel reactor, the product solution collected at the outlet is pumped into the extraction tower. The extraction agent is 600mL of eth...
PUM
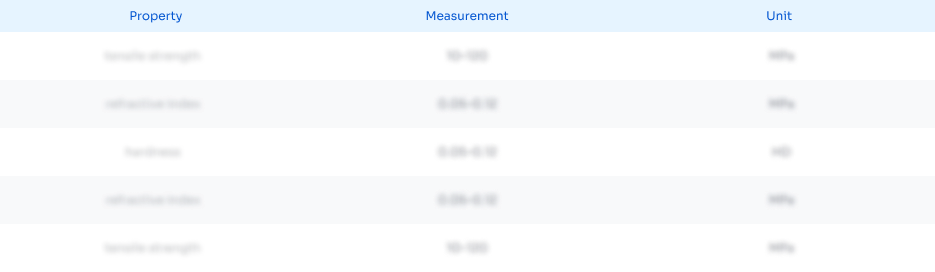
Abstract
Description
Claims
Application Information

- R&D
- Intellectual Property
- Life Sciences
- Materials
- Tech Scout
- Unparalleled Data Quality
- Higher Quality Content
- 60% Fewer Hallucinations
Browse by: Latest US Patents, China's latest patents, Technical Efficacy Thesaurus, Application Domain, Technology Topic, Popular Technical Reports.
© 2025 PatSnap. All rights reserved.Legal|Privacy policy|Modern Slavery Act Transparency Statement|Sitemap|About US| Contact US: help@patsnap.com