Production method of 1,2,3,6-tetrahydrophthalimide
A technology of tetrahydrophthalimide and tetrahydrophthalic anhydride, which is applied in the field of organic chemical synthesis, can solve the problems of increasing equipment, time-consuming and laborious, large heat release, etc., so as to save environmental protection costs and reduce costs , the effect of reducing energy consumption
- Summary
- Abstract
- Description
- Claims
- Application Information
AI Technical Summary
Problems solved by technology
Method used
Image
Examples
Embodiment 1
[0063] Put 300kg of 1,2,3,6-tetrahydrophthalic anhydride in a 500L reactor, cool the jacket with frozen brine to 0°C, and pass ammonia gas under stirring conditions to control the temperature at 13 ℃~18℃, carry out the reaction; when the content of tetrahydrophthalic anhydride in the system is lower than 0.3wt%, the ammonia flow is stopped, the ammonia gas is consumed 50kg, and the reaction intermediate is obtained; after the reaction is completed, the temperature is raised to 135℃ and kept for 2h, so that the reaction generates The intermediate is completely converted, and the water produced is continuously released during the process; finally, the temperature is lowered to 25°C, and 292kg of 1,2,3,6-tetrahydrophthalimide solid is obtained; the content is 98.2wt%, and the melting point is 134 °C, the yield was 97.5%.
Embodiment 2
[0065] Put 1290kg of 1,2,3,6-tetrahydrophthalic anhydride in a 2000L reactor, and cool down to 0°C by feeding frozen brine into the jacket. ℃~18℃, react; react until the content of tetrahydrophthalic anhydride in the system is lower than 0.3wt%, stop passing ammonia, consume 226kg of ammonia gas, and obtain a reaction intermediate; If the intermediate content is lower than 0.5wt%, stop the heat preservation, and the water produced will be continuously released during the process; finally, the temperature will be lowered to 25°C, and 1251kg of 1,2,3,6-tetrahydrophthalimide solid will be obtained; the content is 98.5wt %, the melting point is 134°C, and the yield is 97.0%.
Embodiment 3
[0067] Put 300kg of 1,2,3,6-tetrahydrophthalic anhydride in a 500L reactor, cool the jacket to -15°C by feeding frozen brine into the jacket, feed ammonia under stirring conditions and control the temperature to 0°C~5°C, carry out the reaction; when the content of tetrahydrophthalic anhydride in the system is lower than 0.3wt%, stop the ammonia flow, consume 50kg of ammonia gas, and obtain the reaction intermediate; The generated intermediate was completely converted, and the water produced was continuously removed during the process; finally, the temperature was lowered to 25°C, and 288kg of 1,2,3,6-tetrahydrophthalimide solid was obtained; the content was 97.6wt%, and the melting point was 134°C, the yield is 96.2%.
PUM
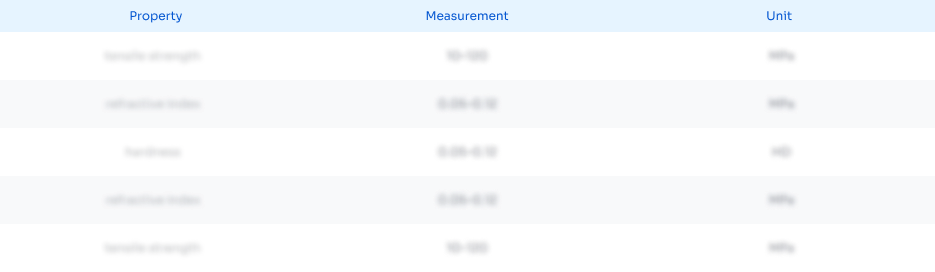
Abstract
Description
Claims
Application Information

- Generate Ideas
- Intellectual Property
- Life Sciences
- Materials
- Tech Scout
- Unparalleled Data Quality
- Higher Quality Content
- 60% Fewer Hallucinations
Browse by: Latest US Patents, China's latest patents, Technical Efficacy Thesaurus, Application Domain, Technology Topic, Popular Technical Reports.
© 2025 PatSnap. All rights reserved.Legal|Privacy policy|Modern Slavery Act Transparency Statement|Sitemap|About US| Contact US: help@patsnap.com