Ultrasonic potential activating method for improving electric casting metal film base interface bonding strength
A technology of interface bonding strength and activation method, which is applied in the direction of electroforming and electrolysis, can solve the problems of insufficient activation of the substrate surface, achieve the effect of improving interface bonding energy, expanding the application range, and increasing the reaction rate
- Summary
- Abstract
- Description
- Claims
- Application Information
AI Technical Summary
Problems solved by technology
Method used
Image
Examples
Embodiment 1
[0057] The present invention is an ultrasonic potential activation method for improving the interface bonding strength of an electroformed metal film, comprising the following steps:
[0058] (1) The copper substrate is treated as a mirror surface by grinding and polishing process. The copper substrate is ultrasonically cleaned in acetone for 20 minutes, then ultrasonically cleaned in ethanol for 20 minutes, rinsed with deionized water and dried with nitrogen, and then placed Dry in an oven at 120°C for 2 hours, take it out and cool to room temperature;
[0059] (2) Spin-coat SU-8 photoresist on the surface of the copper substrate with a desktop glue leveler, the speed is 1450r / min, and the thickness of the obtained film is about 30μm; then use an oven at 85°C for 30min and then cool to room temperature ;Use a UV exposure machine to expose the film for 3 minutes, and the exposure dose is 400mJ / cm 2 , baked in an oven at 85°C for 1 min, then cooled to room temperature, and dev...
Embodiment 2
[0065] The present invention is an ultrasonic potential activation method for improving the interface bonding strength of an electroformed metal film, comprising the following steps:
[0066] (1) The copper substrate is treated as a mirror surface by grinding and polishing process. The copper substrate is ultrasonically cleaned in acetone for 20 minutes, then ultrasonically cleaned in ethanol for 20 minutes, rinsed with deionized water and dried with nitrogen, and then placed Dry in an oven at 120°C for 2 hours, take it out and cool to room temperature;
[0067] (2) Spin-coat SU-8 photoresist on the surface of the copper substrate with a desktop glue leveler, the speed is 1450r / min, and the thickness of the obtained film is about 30μm; then use an oven at 85°C for 30min and then cool to room temperature ;Use a UV exposure machine to expose the film for 3 minutes, and the exposure dose is 400mJ / cm 2 , baked in an oven at 85°C for 1 min, then cooled to room temperature, and dev...
Embodiment 3
[0073] The present invention is an ultrasonic potential activation method for improving the interface bonding strength of an electroformed metal film, comprising the following steps:
[0074] (1) The copper substrate is treated as a mirror surface by grinding and polishing process. The copper substrate is ultrasonically cleaned in acetone for 20 minutes, then ultrasonically cleaned in ethanol for 20 minutes, rinsed with deionized water and dried with nitrogen, and then placed Dry in an oven at 120°C for 2 hours, take it out and cool to room temperature;
[0075] (2) Spin-coat SU-8 photoresist on the surface of the copper substrate with a desktop glue leveler, the speed is 1450r / min, and the thickness of the obtained film is about 30μm; then use an oven at 85°C for 30min and then cool to room temperature ;Use a UV exposure machine to expose the film for 3 minutes, and the exposure dose is 400mJ / cm 2 , baked in an oven at 85°C for 1 min, then cooled to room temperature, and dev...
PUM
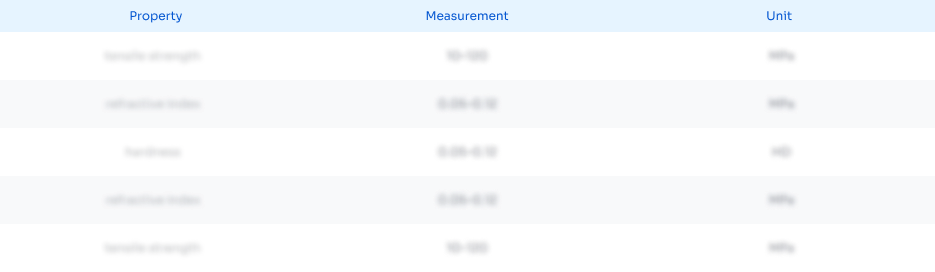
Abstract
Description
Claims
Application Information

- R&D
- Intellectual Property
- Life Sciences
- Materials
- Tech Scout
- Unparalleled Data Quality
- Higher Quality Content
- 60% Fewer Hallucinations
Browse by: Latest US Patents, China's latest patents, Technical Efficacy Thesaurus, Application Domain, Technology Topic, Popular Technical Reports.
© 2025 PatSnap. All rights reserved.Legal|Privacy policy|Modern Slavery Act Transparency Statement|Sitemap|About US| Contact US: help@patsnap.com