Aluminum phosphate gum-based halogen-free high-expansion type flame-retardant heat-insulating fireproof coating material preparation method
An aluminum phosphate gel-based, fire-resistant coating technology, applied in fire-resistant coatings, coatings, etc., can solve the problems of poor fluidity, few reports of all-inorganic fire-resistant coatings, low interface bond strength, etc., and achieve low thermal conductivity. , good interface bonding effect, excellent flame retardant and heat insulation effect
- Summary
- Abstract
- Description
- Claims
- Application Information
AI Technical Summary
Problems solved by technology
Method used
Image
Examples
Embodiment 1
[0024] Example 1 (aluminum phosphate gum-based halogen-free high-expansion flame-retardant heat-insulating fireproof coating suitable for metal materials)
[0025] The preparation method of the aluminum phosphate rubber-based halogen-free high-expansion flame-retardant heat-insulating fireproof coating provided in this example includes the following steps in order:
[0026] (1) Mix ammonium polyphosphate, sodium borate, potassium nitrate, mullite powder, α-alumina, and vermiculite powder according to the mass ratio of 3.5:1:2.5:6:2:0.45, and then put them into a planetary ball mill, Ball mill for 5 hours at a speed of 250r / min to obtain aggregates with fine particle size and uniform mixing;
[0027] (2) Dilute the concentrated phosphoric acid of 85% concentration with water into dilute phosphoric acid of 60% concentration, then put it into a water bath with stirring and heat it to 85°C for subsequent use;
[0028] (3) Slowly add the aluminum hydroxide powder to the dilute pho...
Embodiment 2
[0030] Example 2 (aluminum phosphate gum-based halogen-free high-expansion flame-retardant heat-insulating fireproof coating suitable for wood products)
[0031] (1) Mix ammonium polyphosphate, sodium borate, potassium nitrate, mullite powder, α-alumina, and vermiculite powder according to the mass ratio of 5:0.7:2:7:1:0.1, and then put them into a planetary ball mill, Ball mill for 5 hours at a speed of 250r / min to obtain aggregates with fine particle size and uniform mixing;
[0032] (2) Dilute the concentrated phosphoric acid of 85% concentration with water into dilute phosphoric acid of 60% concentration, then put it into a water bath with stirring and heat it to 85°C for subsequent use;
[0033] (3) Slowly add aluminum hydroxide powder to the dilute phosphoric acid prepared in the above step (2) while stirring, to prevent caking and cause fluidity to drop, wherein the molar ratio of aluminum and phosphorus is 0.75:1, thus preparing A white aluminum phosphate latex liquid...
Embodiment 3
[0035] Example 3 (aluminum phosphate gum-based halogen-free high-expansion flame-retardant heat-insulating fireproof coating suitable for organic products)
[0036] (1) Mix ammonium polyphosphate, sodium borate, potassium nitrate, mullite powder, α-alumina, and vermiculite powder according to the mass ratio of 7:1.3:1.5:6:3:0.1, and then put them into a planetary ball mill, Ball mill for 5 hours at a speed of 250r / min to obtain aggregates with fine particle size and uniform mixing;
[0037] (2) Dilute the concentrated phosphoric acid of 85% concentration with water into dilute phosphoric acid of 60% concentration, then put it into a water bath with stirring and heat it to 80°C for subsequent use;
[0038] (3) Slowly add aluminum hydroxide powder to the dilute phosphoric acid prepared in the above step (2) while stirring, in order to prevent agglomeration from causing a decrease in fluidity, wherein the molar ratio of aluminum to phosphorus is 1:1, thus preparing A white alumi...
PUM
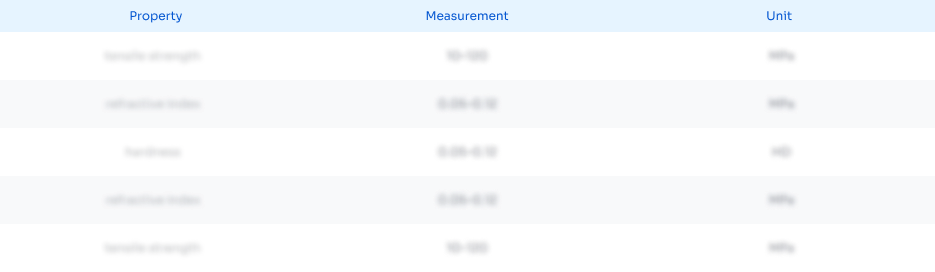
Abstract
Description
Claims
Application Information

- R&D
- Intellectual Property
- Life Sciences
- Materials
- Tech Scout
- Unparalleled Data Quality
- Higher Quality Content
- 60% Fewer Hallucinations
Browse by: Latest US Patents, China's latest patents, Technical Efficacy Thesaurus, Application Domain, Technology Topic, Popular Technical Reports.
© 2025 PatSnap. All rights reserved.Legal|Privacy policy|Modern Slavery Act Transparency Statement|Sitemap|About US| Contact US: help@patsnap.com