Method for enhancing creep resistance of ceramic mold core through customization
A technology for ceramic casting and creep resistance, which is used in ceramic molding machines, casting molds, cores, etc., can solve the problems of affecting the surface roughness of the inner cavity of the casting mold and not using it, and achieves strong shape retention ability and improved resistance. Deformation ability, strength-enhancing effect
- Summary
- Abstract
- Description
- Claims
- Application Information
AI Technical Summary
Problems solved by technology
Method used
Image
Examples
Embodiment 1
[0048] For the up and down straight-through core, the method of customizing and enhancing the creep resistance of the monolithic ceramic casting core includes the following steps:
[0049] 1) SL model design and preparation
[0050] Use UG to design the 3D model of the resin mold, design the fixing holes, refer to figure 1 , figure 2 with image 3 , among which, 1 is the blade body; 2 is the fixing hole; 3 is the up and down straight core; 4 is the shell; 5 is the ceramic rod; The two-dimensional slice file with a thickness of 0.15mm is imported into the light-curing molding equipment to create a resin mold, and the excess resin and support are removed with industrial alcohol and dried.
[0051] 2) Select and insert the ceramic rod
[0052] For cores that run through the top and bottom, refer to figure 2 , Insert a ceramic rod into the fixing hole for interference fit, and fix the bottom end to the bottom of the resin mold with hot melt adhesive. After gel injection mold...
Embodiment 2
[0069] The difference from Example 1 is that, referring to figure 2 , For the core that is straight up and down, design a fixing hole at the bottom of the shell, insert the ceramic rod through it, and then fix it with hot melt adhesive. And for cores that are not straight up and down, such as Figure 4 with Figure 5 , the twist of the core is high, and when the ceramic rod with better rigidity cannot be inserted, fix holes are respectively set at the upper and lower ends of the mold, and the ceramic fiber 7 with good toughness is selected and twisted and inserted into the cavity. The ceramic fiber 7 is oxidized. Aluminum ceramic fiber or silicon carbide ceramic fiber is selected according to the material of the ceramic matrix, such as Image 6 shown, and glued in the fixing holes at both ends with AB glue. All the other processing steps are the same as in Example 1.
PUM
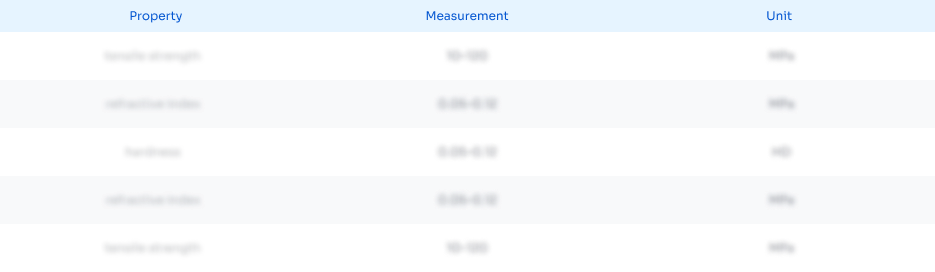
Abstract
Description
Claims
Application Information

- R&D Engineer
- R&D Manager
- IP Professional
- Industry Leading Data Capabilities
- Powerful AI technology
- Patent DNA Extraction
Browse by: Latest US Patents, China's latest patents, Technical Efficacy Thesaurus, Application Domain, Technology Topic, Popular Technical Reports.
© 2024 PatSnap. All rights reserved.Legal|Privacy policy|Modern Slavery Act Transparency Statement|Sitemap|About US| Contact US: help@patsnap.com