Dressing-metallurgy combined method for treating ultra-fine copper sulfide ore
A combined technology of copper sulfide ore, dressing and metallurgy, applied in chemical instruments and methods, grain processing, flotation, etc., can solve the problems of poor recovery index, difficult dissociation of fine particles, easy overgrinding, etc., and achieves high leaching index, Improve flotation recovery rate and avoid overgrinding effect
- Summary
- Abstract
- Description
- Claims
- Application Information
AI Technical Summary
Problems solved by technology
Method used
Image
Examples
Embodiment 1
[0030] A combined dressing and metallurgy method for processing fine-grained copper sulfide ore, such as figure 1 shown, including the following steps:
[0031] S1. Add the raw ore to the rod mill to grind the ore until the fineness is -74 μm, accounting for 80-85%. 3-5 minutes before the grinding time arrives, add the collector isobutyl xanthate potassium ( Produced by SENMIN (Pty) Ltd), based on the dry weight of raw ore, add 120-150g of collector per ton of raw ore;
[0032] S2, the grinding product obtained by grinding in step S1 is fed into the flotation machine, the pulp concentration of the grinding product is adjusted to 25-30%, and the foaming agent SF522 (produced by SENMIN (Pty) Ltd) is added to the flotation machine. The full name is SENFROTH522), according to the dry weight of raw ore, 50-70g of foaming agent is added per ton of raw ore; roughing operation is carried out for 3-5 minutes to obtain copper rough concentrate and roughing tailings;
[0033] S3. Adjus...
Embodiment 2
[0044] In a large-scale foreign copper mine, the copper minerals are mainly copper sulfide minerals such as chalcopyrite and chalcopyrite, and the raw ore contains 6.05% copper. The distribution of the target minerals is fine and uneven, and a single flotation process is adopted It is difficult to obtain a better test beneficiation index. Adopt the method described in embodiment 1 to process in the present embodiment, concrete steps include:
[0045] According to the dry weight of each ton of raw ore, take a certain amount of raw ore and add it to the rod mill for grinding until the fineness is -74μm, accounting for 85%. 5 minutes before the grinding time, add 150g / t of collector isobutyl into the mill Potassium xanthate base; feed the grinding product into the flotation machine, adjust the pulp concentration to 30%, add 70g / t SF522 to the flotation machine, and perform roughing operation for 3 minutes to obtain copper coarse concentrate. Copper coarse concentrate is obtained...
Embodiment 3
[0048] In a large copper mine in Qinghai, the copper minerals are mainly copper sulfide minerals such as chalcopyrite and copper blue. The raw ore contains 2.74% copper, and the target minerals are distributed with fine particle size. Adopt the method described in embodiment 1 to process in the present embodiment, concrete steps include:
[0049] According to the dry weight of each ton of raw ore, take a certain amount of raw ore and add it to the rod mill for grinding until the fineness is -74μm, accounting for 80%. 5 minutes before the grinding time, add 150g / t isobutyl xanthogen to the mill Potassium acid; put the grinding product into the flotation machine, adjust the pulp concentration to 30%, add 70g / t SF522 to the flotation machine, and carry out roughing operation for 3 minutes to obtain copper rough concentrate, which is passed through a blank High-grade copper concentrate No. 1 and medium ore No. 1 were obtained from the quick selection operation, and the slurry conc...
PUM
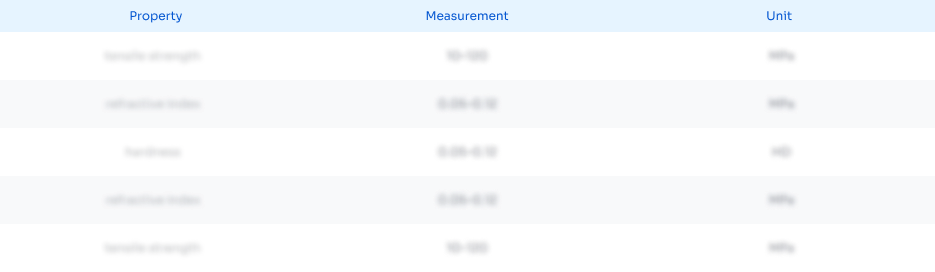
Abstract
Description
Claims
Application Information

- R&D
- Intellectual Property
- Life Sciences
- Materials
- Tech Scout
- Unparalleled Data Quality
- Higher Quality Content
- 60% Fewer Hallucinations
Browse by: Latest US Patents, China's latest patents, Technical Efficacy Thesaurus, Application Domain, Technology Topic, Popular Technical Reports.
© 2025 PatSnap. All rights reserved.Legal|Privacy policy|Modern Slavery Act Transparency Statement|Sitemap|About US| Contact US: help@patsnap.com