Method of preparing PCB with improvement on back hole drilling burrs and small crimping hole
A crimping hole and back-drilling technology, which is applied in multi-layer circuit manufacturing, printed circuit manufacturing, and the formation of electrical connection of printed components, can solve problems such as small crimping holes and achieve the effect of preventing small crimping holes.
- Summary
- Abstract
- Description
- Claims
- Application Information
AI Technical Summary
Problems solved by technology
Method used
Examples
Embodiment
[0019] This embodiment provides a PCB preparation method for improving back-drilled holes and small crimping holes, which includes the following steps: specifically, the following steps are included:
[0020] (1) Cutting: Cut out the double-sided copper clad laminate as the inner core board according to the panel size required by the design.
[0021] (2) Making the inner layer circuit: the inner layer circuit is made on the inner layer core board by adopting the negative process, and the inner layer core board with the inner layer circuit prepared is obtained. Carry out POE punching and inner layer AOI sequentially according to conventional procedures.
[0022] (3) Lamination: pre-press the inner core board, then pre-stack the inner core board, prepreg, and outer copper foil according to the product design, and perform pre-lamination by fusion and / or riveting. Fixing, the layers are pre-fixed together to form a pre-laminated structure, and then the pre-laminated structure is ...
PUM
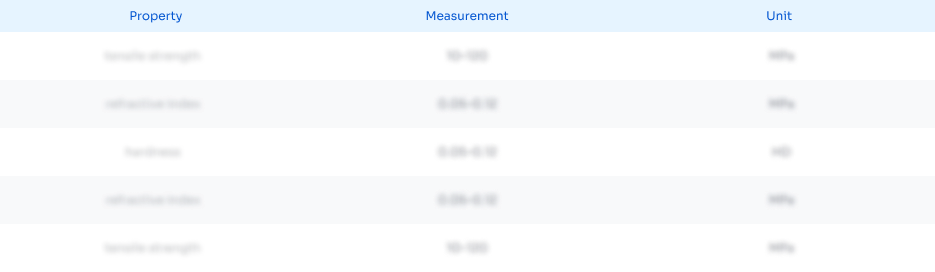
Abstract
Description
Claims
Application Information

- R&D
- Intellectual Property
- Life Sciences
- Materials
- Tech Scout
- Unparalleled Data Quality
- Higher Quality Content
- 60% Fewer Hallucinations
Browse by: Latest US Patents, China's latest patents, Technical Efficacy Thesaurus, Application Domain, Technology Topic, Popular Technical Reports.
© 2025 PatSnap. All rights reserved.Legal|Privacy policy|Modern Slavery Act Transparency Statement|Sitemap|About US| Contact US: help@patsnap.com