Two-component epoxy anticorrosive coating
An epoxy anti-corrosion coating, a two-component technology, applied in the direction of anti-corrosion coatings, epoxy resin coatings, coatings, etc., can solve the problem that the anti-corrosion performance cannot be further improved, and achieve improved anti-corrosion performance, improved corrosion resistance, and anti-corrosion properties. Improved effect
- Summary
- Abstract
- Description
- Claims
- Application Information
AI Technical Summary
Problems solved by technology
Method used
Examples
example 1
[0031] After mixing graphene oxide and water at a mass ratio of 1:10, ultrasonically disperse to obtain a graphene oxide dispersion; then mix the obtained graphene oxide dispersion with sodium polystyrene sulfonate at a mass ratio of 20:1 , at a temperature of 85°C and a stirring speed of 500r / min, heat and stir the reaction, and then concentrate under reduced pressure to obtain a concentrated solution; pump the obtained concentrated solution to a spray dryer, and when the inlet air temperature is 120°C, Under the condition of air outlet temperature of 80°C, atomize and granulate to obtain graphene oxide microspheres; mix potassium carbonate and titanium dioxide in a grinder at a molar ratio of 1.2:4.0, and mix and grind for 30 hours to obtain a mixed powder. The powder was moved into the muffle furnace, and the temperature in the furnace was raised to 850°C at a heating rate of 10°C / min. After heat preservation and calcination for 14 hours, a pretreated mixed powder billet was...
example 2
[0033] Mix potassium carbonate and titanium dioxide in a grinder at a molar ratio of 1.2:4.0, mix and grind for 30 hours to obtain a mixed powder, move the mixed powder into a muffle furnace, and raise the temperature in the furnace at a rate of 10°C / min to After calcination at 850°C for 14 hours, the pretreated mixed powder blank was obtained. After the pretreated mixed powder blank was washed with hydrochloric acid with a mass fraction of 18% for 10 times, and then washed with deionized water for 8 times, the pretreated mixed powder was obtained. Mix the pretreatment mixed powder and hydrochloric acid with a mass fraction of 15% in a beaker at a mass ratio of 1:30, and add aniline 0.6 times the mass of the pretreated mixed powder and 0.5 times the mass of the pretreated powder ethyl orthosilicate to the beaker Esters, after stirring and mixing at a temperature of 50°C and a speed of 400r / min for 5 hours, a mixed dispersion liquid was obtained. Mix the mixed dispersion liquid ...
example 3
[0035] Mix potassium carbonate and titanium dioxide in a grinder at a molar ratio of 1.2:4.0, mix and grind for 30 hours to obtain a mixed powder, move the mixed powder into a muffle furnace, and raise the temperature in the furnace at a rate of 10°C / min to After calcination at 850°C for 14 hours, the pretreated mixed powder blank was obtained. After the pretreated mixed powder blank was washed with hydrochloric acid with a mass fraction of 18% for 10 times, and then washed with deionized water for 8 times, the pretreated mixed powder was obtained. Mix the pretreated mixed powder and hydrochloric acid with a mass fraction of 15% in a beaker at a mass ratio of 1:30, and add mixed metal salt powder 0.5 times the mass of the pretreated mixed powder and 0.5 times the mass of the pretreated powder Ethyl silicate, after stirring and mixing for 5 hours at a temperature of 50°C and a speed of 400r / min, a mixed dispersion liquid was obtained. Mix the mixed dispersion liquid and the init...
PUM
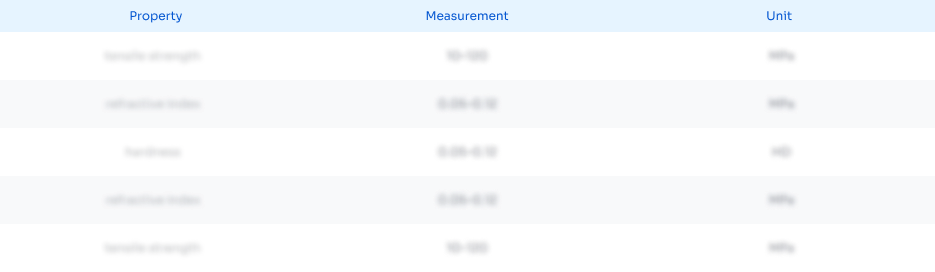
Abstract
Description
Claims
Application Information

- Generate Ideas
- Intellectual Property
- Life Sciences
- Materials
- Tech Scout
- Unparalleled Data Quality
- Higher Quality Content
- 60% Fewer Hallucinations
Browse by: Latest US Patents, China's latest patents, Technical Efficacy Thesaurus, Application Domain, Technology Topic, Popular Technical Reports.
© 2025 PatSnap. All rights reserved.Legal|Privacy policy|Modern Slavery Act Transparency Statement|Sitemap|About US| Contact US: help@patsnap.com