EBM variable direction forming dynamic slicing method cooperated with 840D numerical control system
A numerical control system and direction-changing technology, applied in general control systems, control/adjustment systems, program control, etc., can solve problems such as metal over-accumulation, electron gun vibration, unsuitable for adding supports, etc., to improve formability and reduce calculations the effect of time
- Summary
- Abstract
- Description
- Claims
- Application Information
AI Technical Summary
Problems solved by technology
Method used
Image
Examples
Embodiment Construction
[0068] The present invention provides a dynamic slicing method of EBM variable direction forming in cooperation with 840D numerical control system. The parallel computing technology of the graphics card is used to slice the STL file to improve the speed of data acquisition. Clearance, adjust the layer thickness or forming posture according to the feedback data, without affecting the processing pace. The pivotal movement of the baseplate with the hardware reduces or eliminates the use of supports.
[0069] see figure 1 , the present invention a kind of cooperative 840D numerical control system EBM variable direction forming dynamic slicing method, comprises the following steps:
[0070] S1. Use the GPU slicing method to load voxel information in parallel. When the number of triangular meshes is large, reduce the calculation time, create a vertex array object VAO, open the template buffer, adjust the projection matrix to the slice height when rendering the 3D model, and use re...
PUM
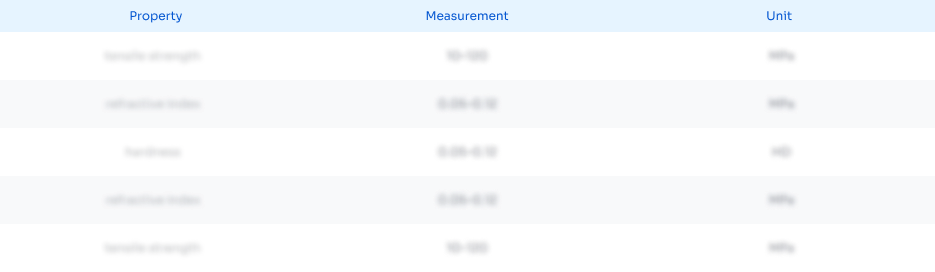
Abstract
Description
Claims
Application Information

- Generate Ideas
- Intellectual Property
- Life Sciences
- Materials
- Tech Scout
- Unparalleled Data Quality
- Higher Quality Content
- 60% Fewer Hallucinations
Browse by: Latest US Patents, China's latest patents, Technical Efficacy Thesaurus, Application Domain, Technology Topic, Popular Technical Reports.
© 2025 PatSnap. All rights reserved.Legal|Privacy policy|Modern Slavery Act Transparency Statement|Sitemap|About US| Contact US: help@patsnap.com