A Centrifugal Spinning Nozzle System for Multifiber Generation
A centrifugal spinning, multi-fiber technology, used in fiber processing, spinneret assemblies, textiles and papermaking, etc., can solve problems such as low manufacturing efficiency
- Summary
- Abstract
- Description
- Claims
- Application Information
AI Technical Summary
Problems solved by technology
Method used
Image
Examples
Embodiment 1
[0047] see Figure 1 to Figure 6 , a centrifugal spinning nozzle system that generates multi-fibers, comprising an injection pipe 1, a spinning head 2 and a driving pipe 3, the bottom of the spinning head 2 is connected to the top of the driving pipe 3, and the spinning head 2 The inside is provided with a material holding chamber 21, and the bottom end of the injection pipe 1 passes through the injection port 22 and communicates with the top of the material holding chamber 21; the centrifugal spinning nozzle system also includes an air receiving shell 4 and a spinning Tube 5, the inside of the spinneret 5 is provided with a spinneret cavity 51, the inner end of the spinneret 5 is connected to the left side of the spinning head 2, the outer end of the spinneret 5 extends outward, and the spinneret The outer end of the tube 5 is provided with a spinneret 52, the spinneret 52 communicates with the material chamber 21 through the spinneret 51, and the number of the spinneret 5 is...
Embodiment 2
[0049] Basic content is the same as embodiment 1, the difference is:
[0050] A spinneret gap 46 is provided between the spinneret 52 and the outer end of the finger holder cavity 44 . The width of the hollow shell finger 43 is smaller than the width of the right hollow shell portion 42 , and a finger gap 47 is provided between the inner end of the hollow shell finger 43 and the left side of the spinning head 2 .
Embodiment 3
[0052] Basic content is the same as embodiment 1, the difference is:
[0053] The inside of the driving tube 3 is provided with a tube lumen 31, and the tube wall 32 located in the left receiving air cavity 411 on the driving tube 3 is provided with a side air passage 33, and the tube lumen 31 connects with the left receiving air cavity 411 through the side air passage 33. connected. The number of the side air passages 33 is four, and all the side air passages 33 are evenly arranged around the tube wall 32 , and the top view shape of the side air passages 33 is fan-shaped.
PUM
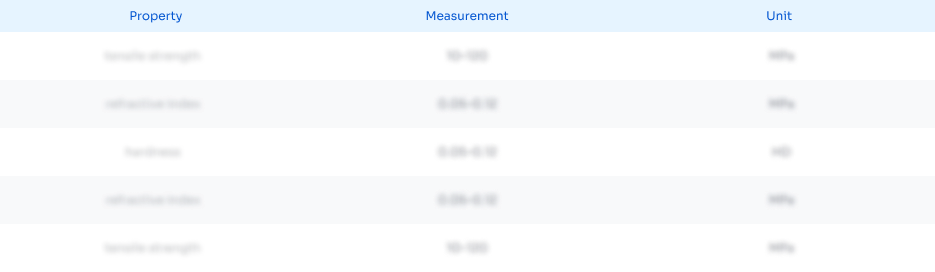
Abstract
Description
Claims
Application Information

- R&D
- Intellectual Property
- Life Sciences
- Materials
- Tech Scout
- Unparalleled Data Quality
- Higher Quality Content
- 60% Fewer Hallucinations
Browse by: Latest US Patents, China's latest patents, Technical Efficacy Thesaurus, Application Domain, Technology Topic, Popular Technical Reports.
© 2025 PatSnap. All rights reserved.Legal|Privacy policy|Modern Slavery Act Transparency Statement|Sitemap|About US| Contact US: help@patsnap.com