Semiconductor substrate material polishing method
A substrate material and semiconductor technology, applied in the direction of cleaning methods using liquids, cleaning methods and utensils, chemical instruments and methods, etc., can solve the problems of not improving the chemical mechanical polishing rate, and achieve short polishing process time and laser polishing time Effect of short, reduced processing steps
- Summary
- Abstract
- Description
- Claims
- Application Information
AI Technical Summary
Problems solved by technology
Method used
Image
Examples
Embodiment 1
[0028] The surface of the silicon carbide substrate after wire-cutting is polished by the GYLPM type nanosecond laser of IPG company: the laser scanning speed is 1mm / s, and the laser energy density used is 1J / cm 2 After the scanning is completed, put it in ethanol and ultrasonically clean it for 5 minutes; use the 1000S polishing machine of Shenyang Kejing Company, alkaline alumina polishing liquid, and polyurethane polishing pad to polish the cleaned silicon carbide substrate for 3 hours, and the polishing pressure is 400g / cm 2 . After polishing, a Leica microscope was used to observe the surface of the polished silicon carbide material, and it was found that the surface damage had been completely removed.
Embodiment 2
[0030] Universal company ULR50 type CO 2 The surface of the silicon carbide substrate after laser polishing and wire cutting: the laser scanning speed is 250mm / s, and the laser energy density used is 0.01J / cm 2 After the scanning is completed, put it in ethanol for ultrasonic cleaning for 1 minute; use the 1000S polishing machine of Shenyang Kejing Company, alkaline cerium oxide polishing liquid, and composite polishing pad to polish the cleaned silicon carbide substrate for 1 hour, and the polishing pressure is 100g / cm 2 . After polishing, a Leica microscope was used to observe the surface of the polished silicon carbide material, and it was found that the surface damage had been completely removed.
Embodiment 3
[0032] The silicon carbide substrate surface after wire-cutting is polished by LIGHTCINVERSION PH1 femtosecond laser: the laser scanning speed is 500mm / s, and the laser energy density used is 20J / cm 2 ; After the scanning is completed, put it in water for ultrasonic cleaning for 10 minutes; use the 1000S polishing machine of Shenyang Kejing Company, acidic silicon oxide polishing liquid, and polyurethane polishing pad to polish the cleaned silicon carbide substrate for 5 hours, and the polishing pressure is 300g / cm 2 . After polishing, a Leica microscope was used to observe the surface of the polished silicon carbide material, and it was found that the surface damage had been completely removed.
PUM
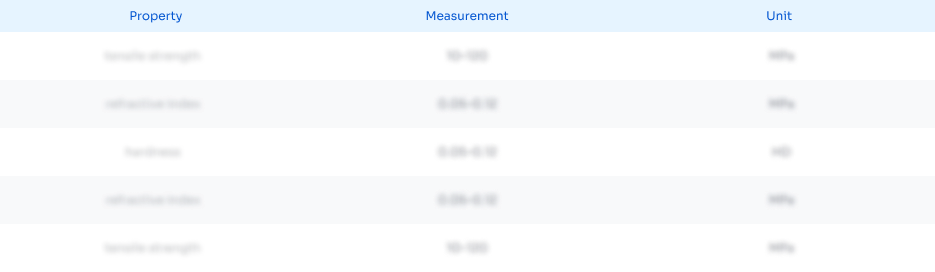
Abstract
Description
Claims
Application Information

- R&D
- Intellectual Property
- Life Sciences
- Materials
- Tech Scout
- Unparalleled Data Quality
- Higher Quality Content
- 60% Fewer Hallucinations
Browse by: Latest US Patents, China's latest patents, Technical Efficacy Thesaurus, Application Domain, Technology Topic, Popular Technical Reports.
© 2025 PatSnap. All rights reserved.Legal|Privacy policy|Modern Slavery Act Transparency Statement|Sitemap|About US| Contact US: help@patsnap.com