Method of flotation and magnesium reduction for talcum-type copper-nickel sulfide ore
A copper-nickel sulfide ore, flotation technology, applied in the field of metallurgy, can solve the problems of affecting the progress, over-crushing of gangue minerals, low hardness, etc., and achieve the effect of enhancing selectivity and reducing MgO content
- Summary
- Abstract
- Description
- Claims
- Application Information
AI Technical Summary
Problems solved by technology
Method used
Image
Examples
Embodiment 1
[0029] Raw material: a sample of a low-grade talc-type copper-nickel sulfide ore in Xinjiang. The grade of Ni in the ore is 0.35%, the grade of Cu is 0.18%, and the content of MgO is 26.87%.
[0030] The process is:
[0031] The fineness of the ore grinding operation is -0.074mm and the content is 75%. Sodium carbonate is added 1000g / t during the grinding process; 200g / t sodium hexametaphosphate and 80g butyl xanthate are added to the slurry obtained by grinding. / t, butyl ammonium black medicine 40g / t, acidified water glass 500g / t, sodium carboxymethyl cellulose 300g / t, 2# oil 20g / t, flotation and separation operation; The two roughing operations of copper-nickel sulfide minerals are carried out in stages by adding chemicals. The second roughing is followed by acidification of water glass 100g / t, sodium carboxymethyl cellulose 50g / t, and butyl xanthate 20g / t. Butylammonium black medicine 10g / t, 2# oil 10g / t, combine the two sorted foam products as coarse concentrate for processin...
Embodiment 2
[0037] Raw material: a low-grade talc-type copper-nickel sulfide ore sample in Hami, with the Ni grade of 0.42%, the Cu grade of 0.29% and the MgO content of 28.57% in the original ore.
[0038] The process is:
[0039] 1) Preparation and grinding of ore: The fineness of the ore for grinding operation is -0.074mm, the content is 75%, and the sodium carbonate is added 2000g / t during the grinding process;
[0040] 2) Pulping: Add 190g / t of sodium hexametaphosphate, 480g / t of acidified water glass, 350g / t of sodium carboxymethyl cellulose, 150g / t of butyl xanthate, and butyl xanthate into the pulp obtained by grinding in step 1. Ammonium black medicine 15g / t, 2# oil dosage is 20g / t;
[0041] 3) Flotation separation:
[0042] (1) Carry out the rough selection of copper-nickel sulfide minerals on the slurry after adding the chemical slurry in step 2,
[0043] (2) The rough tailings were scanned four times, and 140g / t of acidified water glass was added sequentially in the first sweep, the dos...
Embodiment 3
[0048] Raw material: a sample of a talc-type copper-nickel sulfide ore in Shaanxi. The grade of Ni in the ore is 0.62%, the grade of Cu is 0.38%, and the content of MgO is 27.58%.
[0049] The process is:
[0050] The fineness of the ore grinding operation is -0.074mm and the content is 75%. Sodium carbonate is added 1500g / t during the grinding process; the dispersant sodium hexametaphosphate 100g / t is added to the slurry obtained by grinding successively to collect 60g / t of butyl xanthate and 20g / t of butyl ammonium black medicine, 300g / t of inhibitor acidified water glass and 200g / t of sodium carboxymethyl cellulose, foaming agent 2# oil 20g / t, flotation separation Operation: Two roughing operations of copper-nickel sulfide minerals are carried out on the slurry after adding chemicals to the slurry, adopting the stage dosing stage to select, and the second roughing is followed by adding 100g / t acidified water glass and sodium carboxymethyl cellulose 50g / t, butyl xanthate 20g / t, ...
PUM
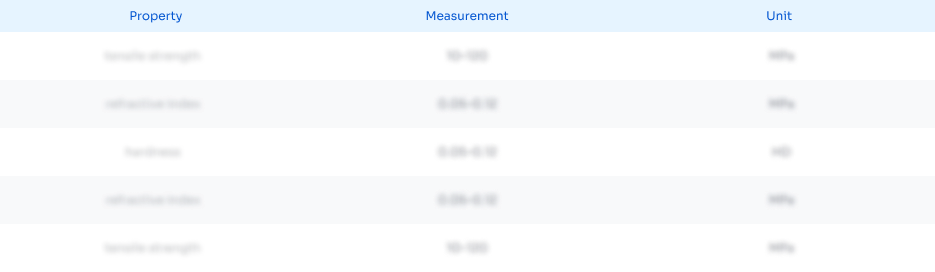
Abstract
Description
Claims
Application Information

- R&D
- Intellectual Property
- Life Sciences
- Materials
- Tech Scout
- Unparalleled Data Quality
- Higher Quality Content
- 60% Fewer Hallucinations
Browse by: Latest US Patents, China's latest patents, Technical Efficacy Thesaurus, Application Domain, Technology Topic, Popular Technical Reports.
© 2025 PatSnap. All rights reserved.Legal|Privacy policy|Modern Slavery Act Transparency Statement|Sitemap|About US| Contact US: help@patsnap.com