Selective oxygen pressure leaching method for the enrichment of precious metals from high-iron, high-copper and nickel-containing materials
An oxygen pressure leaching and precious metal technology, which is applied to the system of selective oxygen pressure leaching and enriching of precious metals for high iron and high copper nickel-containing materials. Open circuit, long process flow, precious metal dispersion loss, etc.
- Summary
- Abstract
- Description
- Claims
- Application Information
AI Technical Summary
Problems solved by technology
Method used
Image
Examples
Embodiment 1
[0114] A kind of high-speed iron with the composition (%) of: Ni~30, Cu~20, Fe~20, Co~0.7, S~25, ∑Pt (including Au, Pd, Pt, the same below)~10g / t, The method for enriching precious metals by selective oxygen pressure leaching of copper-nickel-containing materials comprises the following processing steps:
[0115] S10. Purification and impurity removal, mixing oxygen pressure iron removal solution and oxygen pressure leaching nickel solution to prepare pre-purification and impurity removal liquid, mixing and stirring the prepared pre-purification and impurity removal liquid with iron-high-copper-nickel minerals, and slurrying initial Cu 2+ The concentration is 10g / L, the liquid-solid ratio is 6:1, and the slurrying time is 1h. The purification and impurity removal process controls the temperature at 85°C and the air volume at 1500NM 3 / t of material, the time for purification and removal of impurities is 6 hours, and the pH value of the end point of the removal reaction is 6.0...
Embodiment 2
[0121] A selective oxygen pressure leaching enrichment of high-iron, high-copper and nickel-containing materials with the composition (%): Ni~60, Cu~5, Fe~15, Co~1.2, S~12, ∑Pt~110g / t A method for precious metals comprising the following processing steps:
[0122] S10. Purification and impurity removal, mixing oxygen pressure iron removal solution and oxygen pressure leaching nickel solution to prepare pre-purification and impurity removal liquid, mixing and stirring the prepared pre-purification and impurity removal liquid with iron-high-copper-nickel minerals, and slurrying initial Cu 2+ The concentration is 10g / L, the liquid-solid ratio is 8:1, and the slurrying time is 1h. The purification and impurity removal process controls the temperature at 85°C and the air volume at 1500NM 3 / t of material, the purification and removal time is 6h, and the pH value at the end of the removal reaction is 5.9. After purification and removal of impurities, the slurry is subjected to liq...
Embodiment 3
[0128] A selective oxygen pressure leaching enrichment of high-iron, high-copper and nickel-containing materials with the composition (%) of: Ni~40, Cu~15, Fe~15, Co~2.5, S~25, ∑Pt~20g / t A method for precious metals comprising the following processing steps:
[0129] S10. Purification and impurity removal, mixing oxygen pressure iron removal solution and oxygen pressure leaching nickel solution to prepare pre-purification and impurity removal liquid, mixing and stirring the prepared pre-purification and impurity removal liquid with iron-high-copper-nickel minerals, and slurrying initial Cu 2+ The concentration is 8g / L, the liquid-solid ratio is 6:1, and the slurrying time is 1h. The purification and impurity removal process controls the temperature at 85°C and the air volume at 1500NM 3 / t of material, the purification and removal time is 6h, and the pH value at the end of the removal reaction is 6.2. After purification and removal of impurities, the slurry is subjected to l...
PUM
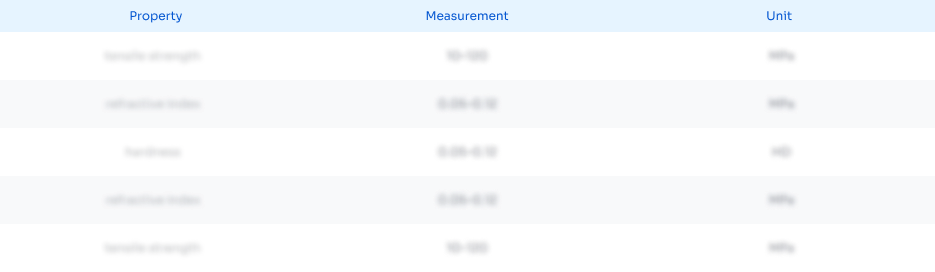
Abstract
Description
Claims
Application Information

- R&D
- Intellectual Property
- Life Sciences
- Materials
- Tech Scout
- Unparalleled Data Quality
- Higher Quality Content
- 60% Fewer Hallucinations
Browse by: Latest US Patents, China's latest patents, Technical Efficacy Thesaurus, Application Domain, Technology Topic, Popular Technical Reports.
© 2025 PatSnap. All rights reserved.Legal|Privacy policy|Modern Slavery Act Transparency Statement|Sitemap|About US| Contact US: help@patsnap.com