Manganese dioxide recovery method by waste lithium ion battery powder selective lithium-extracting and electrolytic separation
A lithium-ion battery, manganese dioxide technology, applied in battery recycling, waste collector recycling, electrolysis process and other directions, can solve the problems of high production cost, low lithium recovery rate, difficult separation of lithium and sodium, etc., to achieve high-efficiency separation, quality excellent effect
- Summary
- Abstract
- Description
- Claims
- Application Information
AI Technical Summary
Problems solved by technology
Method used
Image
Examples
Embodiment 1
[0027] Such as figure 1 As shown, the present embodiment provides a method for selectively extracting lithium from waste lithium-ion battery powder and electrolytically separating and recovering manganese dioxide. The specific steps include the following:
[0028] (1) Mature roasting: using waste ternary lithium-ion battery powder as raw material, its main composition is Li4.38%, Ni18.72%, Co7.87%, Mn11.23%, Cu0.63%, Fe0.25% , Al0.92%. Weigh a certain amount of waste lithium-ion battery powder, add it according to n H2SO4 :n Li =0.95 (molar ratio) Slowly add concentrated sulfuric acid and stir evenly, then put it into an electric furnace and bake at 550°C for 2h, take out the calcined sand and cool it to room temperature, and then grind it evenly.
[0029] (2) Water immersion: put the evenly ground calcined sand into the leaching reactor, add pure water, mechanically stir and leaching for 3 hours at a liquid-solid ratio of 4:1, and a temperature of 60°C, and filter and sepa...
Embodiment 2
[0035] Such as figure 1 As shown, the present embodiment provides a method for selectively extracting lithium from waste lithium-ion battery powder and electrolytically separating and recovering manganese dioxide. The specific steps include the following:
[0036] (1) Slaking and roasting: use waste ternary and lithium cobalt oxide mixed battery powder as raw material, control its main composition as Li6.76%, Ni14.43%, Co42.56%, Mn10.86%, Cu0.42%, Fe0.15%, Al0.38%. Weigh a certain amount of waste lithium-ion battery mixed powder, add it according to n H2SO4 :n Li =1.1 (molar ratio) Slowly add concentrated sulfuric acid and stir evenly, then put it into an electric furnace and bake at 650°C for 2h, take out the calcined sand and cool it to room temperature, and then grind it evenly.
[0037] (2) Water immersion: put the evenly ground calcine into the leaching reactor, add pure water, mechanically stir and leaching for 5 hours at a liquid-solid ratio of 3:1, and a temperature...
Embodiment 3
[0043] Such as figure 1 As shown, the present embodiment provides a method for selectively extracting lithium from waste lithium-ion battery powder and electrolytically separating and recovering manganese dioxide. The specific steps include the following:
[0044] (1) Slaking and roasting: use waste ternary and lithium manganate mixed battery powder as raw material, control its main composition as Li6.25%, Ni15.23%, Co12.56%, Mn49.79%, Cu0.53%, Fe0.12%, Al0.36%. Weigh a certain amount of waste lithium-ion battery mixed powder, add it according to n H2SO4 :n Li =1.5 (molar ratio) Slowly add concentrated sulfuric acid and stir evenly, then put it into an electric furnace and bake at 750°C for 4h, take out the calcined sand and cool it to room temperature, and grind it evenly.
[0045] (2) Water immersion: put the evenly ground calcine into the leaching reactor, add pure water, mechanically stir and leaching for 2 hours at a liquid-solid ratio of 8:1, and a temperature of 90°C...
PUM
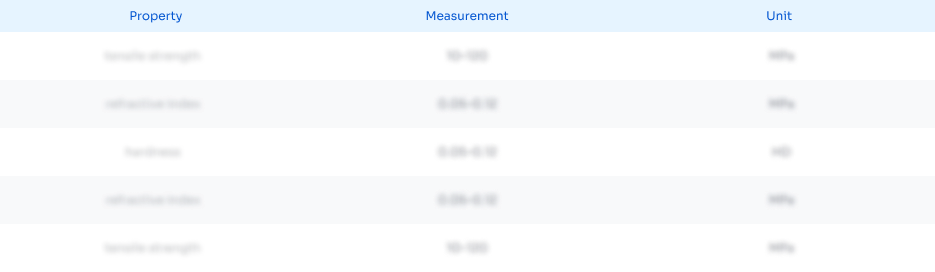
Abstract
Description
Claims
Application Information

- R&D
- Intellectual Property
- Life Sciences
- Materials
- Tech Scout
- Unparalleled Data Quality
- Higher Quality Content
- 60% Fewer Hallucinations
Browse by: Latest US Patents, China's latest patents, Technical Efficacy Thesaurus, Application Domain, Technology Topic, Popular Technical Reports.
© 2025 PatSnap. All rights reserved.Legal|Privacy policy|Modern Slavery Act Transparency Statement|Sitemap|About US| Contact US: help@patsnap.com