Fire-refining method of crude bismuth
A technology of pyro-refining and coarse bismuth, which is applied in the field of pyrometallurgy, can solve problems such as polluting the operating environment, affecting the direct yield of bismuth, and complicated processing procedures, and achieves high direct yield, improved direct yield, and simple equipment Effect
- Summary
- Abstract
- Description
- Claims
- Application Information
AI Technical Summary
Problems solved by technology
Method used
Image
Examples
Embodiment 1
[0023] Such as figure 1 Shown, the method for this thick bismuth fire refining, its concrete steps are as follows:
[0024] (1) First, 800kg of crude bismuth (Bi93.50wt%, Pb5.73wt%, Ag0.64wt%, As0.215wt%, Sb0.134wt%, Cu0.433wt%, Te0. 164wt%) after melting and removing copper until the copper content in the rough bismuth is 0.0015wt%; the process of melting and removing copper is to melt the rough bismuth in the melting pot and remove the molten slag at 600 ° C, and the temperature drops to 500 Remove the copper slag for the first time at ℃, and remove the copper slag for the second time when the temperature drops to 350℃;
[0025] (2) Distill the crude bismuth after copper removal in step (1) under the conditions of pressure 10~30Pa and temperature 1050°C for 8 hours to obtain a crude bismuth (Bi98.99wt%, Pb0.63wt%, Ag0.008wt%) %, Sb0.011wt%, Te0.0033wt%, As0.0015wt%) and high silver coarse bismuth (Bi55.38wt%, Pb15.44wt%, Ag25.28wt%, Sb1.634wt%, Te0.844wt%, As0. 533wt%), ...
Embodiment 2
[0028] Such as figure 1 Shown, the method for this thick bismuth fire refining, its concrete steps are as follows:
[0029] (1) First, 1t of coarse bismuth (Bi82.65wt%, Pb11.77wt%, Ag1.04wt%, As0.65wt%, Sb0.55wt%, Cu0.53wt%, Te0. 76wt%) after melting and removing copper until the copper content in the rough bismuth is 0.0027wt%; the process of melting and removing copper is to melt the rough bismuth in the melting pot and remove the molten slag at 620 ° C, and the temperature drops to 530 Remove the copper slag for the first time at ℃, and remove the copper slag for the second time when the temperature drops to 370°C;
[0030] (2) The crude bismuth after the copper removal in step (1) is vacuum distilled for 12 hours at a pressure of 5~40Pa and a temperature of 1100°C to obtain a crude bismuth (Bi98.28wt%, Pb1.42wt%, Ag0.013wt%) %, Sb0.084wt%, Te0.0064wt%, As0.0022wt%) and high silver coarse bismuth (Bi33.92wt%; Pb24.86wt%; Ag34.65wt%; Sb1.46wt%; Te1.55wt%, As1. 03wt%), hi...
Embodiment 3
[0033] Such as figure 1 Shown, the method for this thick bismuth fire refining, its concrete steps are as follows:
[0034] (1) First, 500kg of crude bismuth (Bi96.34wt%, Pb2.31wt%, Ag0.34wt%, As0.27wt%, Sb0.083wt%, Cu0.12wt%, Te0. 11wt%) after melting and removing copper until the copper content in the rough bismuth is 0.0013wt%; the process of melting and removing copper is to melt the rough bismuth in the melting pot and remove the molten slag at 620°C, and the temperature drops to 510°C Remove the copper slag for the first time at ℃, and remove the copper slag for the second time when the temperature drops to 380°C;
[0035] (2) The crude bismuth after the copper removal in step (1) was vacuum distilled for 6 hours at a pressure of 10~30Pa and a temperature of 1000°C to obtain a crude bismuth (Bi99.26wt%, Pb0.44wt%, Ag0.005wt%) %, Sb0.54wt%, Te1.32wt%, As1.47wt%) and high silver coarse bismuth (Bi63.22wt%, Pb12.35wt%, Ag20.74wt%, Sb0.003wt%, Te0.0016wt%, As0. 0017wt%),...
PUM
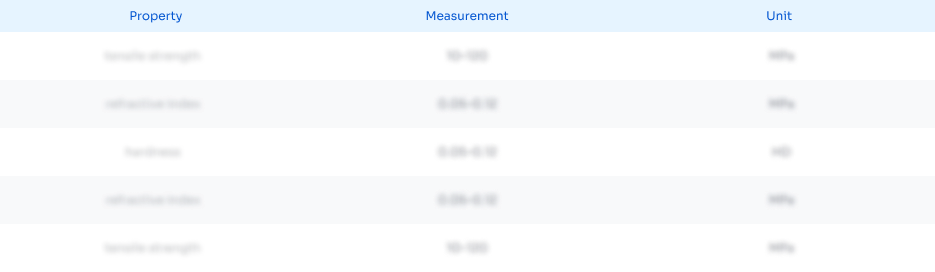
Abstract
Description
Claims
Application Information

- R&D Engineer
- R&D Manager
- IP Professional
- Industry Leading Data Capabilities
- Powerful AI technology
- Patent DNA Extraction
Browse by: Latest US Patents, China's latest patents, Technical Efficacy Thesaurus, Application Domain, Technology Topic, Popular Technical Reports.
© 2024 PatSnap. All rights reserved.Legal|Privacy policy|Modern Slavery Act Transparency Statement|Sitemap|About US| Contact US: help@patsnap.com