Graphene anticorrosive coating used in marine environment and preparation method of coating
A technology for anti-corrosion coatings and marine environments, applied in anti-corrosion coatings, epoxy resin coatings, coatings, etc., can solve the problems of easy reaction, weak anti-microbial corrosion and mold corrosion, and affect the service life of coatings, etc., to achieve Effect of improving microbial corrosion and mold corrosion, improving anti-corrosion performance, and excellent environmental resistance
- Summary
- Abstract
- Description
- Claims
- Application Information
AI Technical Summary
Problems solved by technology
Method used
Image
Examples
Embodiment 1
[0023] The preparation method for the anticorrosion paint of marine environment comprises the following steps:
[0024] S100, take 2.5g of graphite powder with a particle size of 30um, 1.25g of sodium nitrate, 60mL of concentrated sulfuric acid with a mass fraction of 98%, control the temperature of the system at 0-5°C under an ice-water bath, stir for 5 minutes, and then add them evenly within about 15 minutes 7.5g of potassium permanganate, kept for 5min, then removed from the ice water bath, and kept in a warm water bath at about 35°C for 4h. Then 115 mL of deionized water was added dropwise for about 30 minutes, and then heated to 98°C and kept for about 15 minutes. Remove the heat, add deionized water to dilute to 350mL (approximately 180mL), stir for 30min, add 13mL of hydrogen peroxide, react for 15min, centrifuge (7900r / min, 8min) several times, wash with water until the solution is neutral, and wash twice with alcohol , 60°C vacuum drying for 24h to obtain graphite o...
Embodiment 2
[0031] The preparation method for the anticorrosion paint of marine environment comprises the following steps:
[0032] S100, take 2g of graphite powder with a particle size of 30um, 2g of sodium nitrate, and 30mL of concentrated sulfuric acid with a mass fraction of 98%. Potassium manganate, kept for 3 minutes, then removed from the ice water bath, and kept in a warm water bath at about 35°C for 2 hours. Then add 100mL of deionized water dropwise for about 30 minutes, then heat to 98°C and keep it for about 10 minutes. Remove the heat, add deionized water to dilute to 350mL (approximately 180mL), add 10mL hydrogen peroxide after stirring for 30min, react for 10min, centrifuge (7900r / min, 6min) several times, wash with water until the solution is neutral, and wash twice with alcohol , 60°C vacuum drying for 22h to obtain graphite oxide (GTO).
[0033] Weigh a certain amount of GTO powder, according to the ratio of 0.5g / 100mL, add it to NaOH (sodium hydroxide) aqueous solutio...
Embodiment 3
[0039] The preparation method for the anticorrosion paint of marine environment comprises the following steps:
[0040] S100, take 4.6g of graphite powder with a particle size of 30um, 4.2g of sodium nitrate, and 15mL of concentrated sulfuric acid with a mass fraction of 98%, and control the system temperature at 0-5°C under an ice-water bath. After stirring for 12 minutes, add them evenly within about 15 minutes 10g of potassium permanganate, kept for 10min, then removed from the ice water bath, and kept in a warm water bath at about 35°C for 6h. Then 130 mL of deionized water was added dropwise for about 35 minutes, and then heated to 98°C and kept for about 20 minutes. Remove the heat, add deionized water to dilute to 360mL (approximately 180mL), add 15mL hydrogen peroxide after stirring for 40min, react for 20min, centrifuge (7900r / min, 10min) several times, wash with water until the solution is neutral, and wash twice with alcohol , 60 ℃ vacuum drying for 26h to obtain g...
PUM
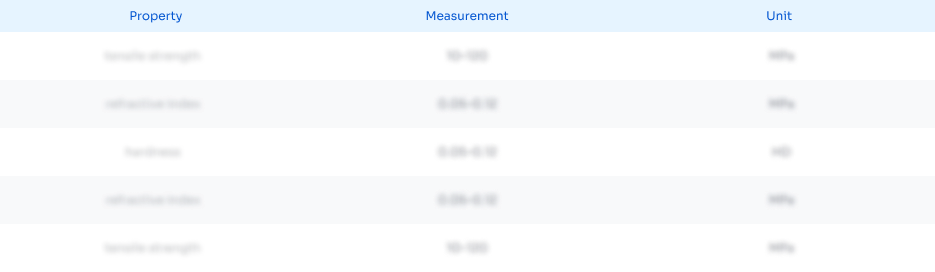
Abstract
Description
Claims
Application Information

- R&D Engineer
- R&D Manager
- IP Professional
- Industry Leading Data Capabilities
- Powerful AI technology
- Patent DNA Extraction
Browse by: Latest US Patents, China's latest patents, Technical Efficacy Thesaurus, Application Domain, Technology Topic, Popular Technical Reports.
© 2024 PatSnap. All rights reserved.Legal|Privacy policy|Modern Slavery Act Transparency Statement|Sitemap|About US| Contact US: help@patsnap.com