Production method of high-solid-content ultra-high-molecular-weight acrylic ester copolymer emulsion
An ultra-high molecular weight, acrylate technology, applied in the production field of high solid content ultra-high molecular weight acrylate copolymer emulsion, can solve the problems of difficulty in reducing product density, insufficient melt strength, small molecular weight, etc. Effects of strength and balance torque, increased emulsion stability, and increased molecular weight
- Summary
- Abstract
- Description
- Claims
- Application Information
AI Technical Summary
Problems solved by technology
Method used
Image
Examples
Embodiment 1
[0044] The production method of the described high solid content ultra-high molecular weight acrylate copolymer emulsion, the steps are as follows:
[0045] (1) 80 parts by weight of water, 0.1 parts by weight of emulsifying dispersant sodium pyrophosphate, 0.5 parts by weight of emulsifying agent sodium lauryl sulfate, 0.01 parts by weight of wetting agent sodium diisobutylnaphthalene sulfonate, 0.02 parts by weight Add the pH regulator sodium bicarbonate into the normal pressure reactor, start stirring, control the rotation speed at 200r / min, and raise the temperature to 55°C;
[0046] (2) 100 parts by weight of monomers (1 part by weight of functional monomer isooctyl acrylate, 5 parts by weight of butyl acrylate, and 94 parts by weight of methyl methacrylate) are added to the reactor, and oxygen is exhausted with nitrogen;
[0047] (3) Heat up to 40°C at a stirring speed of 200r / min, add 0.01 parts by weight of redox initiator (including 0.005 part of oxidant potassium per...
Embodiment 2
[0049] The production method of the described high solid content ultra-high molecular weight acrylate copolymer emulsion, the steps are as follows:
[0050](1) 100 parts by weight of water, 0.9 parts by weight of emulsifying dispersant colloidal silicon dioxide, 3.0 parts by weight of emulsifier sodium dodecylbenzenesulfonate, 0.01 parts by weight of wetting agent NNO (methylene bis-naphthalenesulfonic acid Sodium), 0.02 parts by weight of pH regulator ammonia water (content 28%) are added to the normal pressure reactor, start stirring, control the rotating speed of 150r / min, and heat up to 50°C;
[0051] (2) 100 parts by weight of monomers (5 parts by weight of functional monomer butyl methacrylate, 35 parts by weight of butyl acrylate, and 60 parts by weight of methyl methacrylate) were added to the reactor, and oxygen was exhausted with nitrogen;
[0052] (3) Warm up to 38°C at a stirring speed of 150r / min, add 0.05 parts by weight of a redox initiator (0.025 parts of ammon...
Embodiment 3
[0054] The production method of the described high solid content ultra-high molecular weight acrylate copolymer emulsion, the steps are as follows:
[0055] (1) With 100 parts by weight of water, 0.6 parts by weight of emulsifying dispersant nano silicon dioxide, 2.0 parts by weight of emulsifier (wherein, 1.5 parts by weight of sodium lauryl sulfate, 0.5 parts by weight of sodium dodecylbenzenesulfonate ), 0.02 parts by weight of wetting agent (sodium dialkyl succinate sulfonate), 0.15 parts by weight of pH regulator ammonia (content 25%) are added to the normal pressure reactor, and the stirring is started, and the control speed is 100r / min, and the temperature is raised to 52°C;
[0056] (2) 100 parts by weight of monomers (3 parts by weight of functional monomer butyl methacrylate, 17 parts by weight of butyl acrylate, and 80 parts by weight of methyl methacrylate) were added to the reactor, and oxygen was exhausted with nitrogen;
[0057] (3) Warm up to 39°C at a stirrin...
PUM
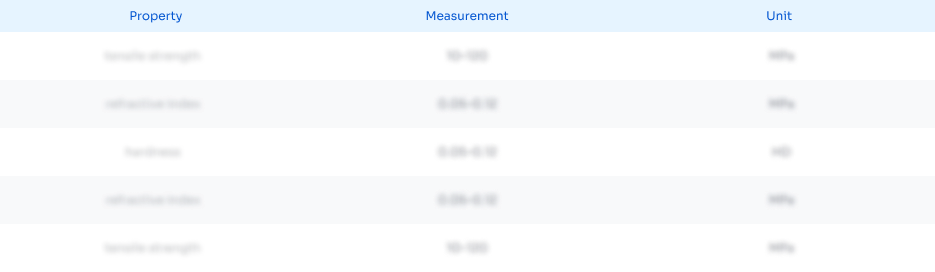
Abstract
Description
Claims
Application Information

- R&D
- Intellectual Property
- Life Sciences
- Materials
- Tech Scout
- Unparalleled Data Quality
- Higher Quality Content
- 60% Fewer Hallucinations
Browse by: Latest US Patents, China's latest patents, Technical Efficacy Thesaurus, Application Domain, Technology Topic, Popular Technical Reports.
© 2025 PatSnap. All rights reserved.Legal|Privacy policy|Modern Slavery Act Transparency Statement|Sitemap|About US| Contact US: help@patsnap.com