Oxidation fiber manufacturing method and oxidation fiber
A technology for oxidizing fibers and manufacturing methods, applied in the directions of fiber chemical characteristics, fiber processing, radiation wave/microwave fiber processing, etc., can solve the problems of excessive pre-oxidation, lack of pre-oxidation of the original fiber, time-consuming and other problems, and achieve improved performance. , the effect of reducing the oxidation time
- Summary
- Abstract
- Description
- Claims
- Application Information
AI Technical Summary
Problems solved by technology
Method used
Image
Examples
Embodiment Construction
[0069] The present invention mainly provides a method for manufacturing oxidized fibers that can effectively shorten the oxidation time of oxidized fibers, effectively reduce the skin-core structure of oxidized fibers, and even make oxidized fibers achieve no obvious skin-core structure, and oxidized fibers related thereto. like figure 2 and image 3 As shown, the oxidation fiber manufacturing method of the present invention basically comprises the following steps:
[0070] a. Provide a conveying unit 30 and a microwave processing unit 40; during implementation, the conveying unit 30 is provided with a feeding unit 31 for providing a fiber yarn bundle 20, and a rewinder for dragging the fiber yarn bundle 20 for continuous transmission The unit 32, a furnace body 33 for the fiber yarn bundle 20 to pass through, wherein the fiber yarn bundle 20 can be composed of a fiber (not shown in the figure) or a plurality of the fibers assembled into a bundle; the microwave processing un...
PUM
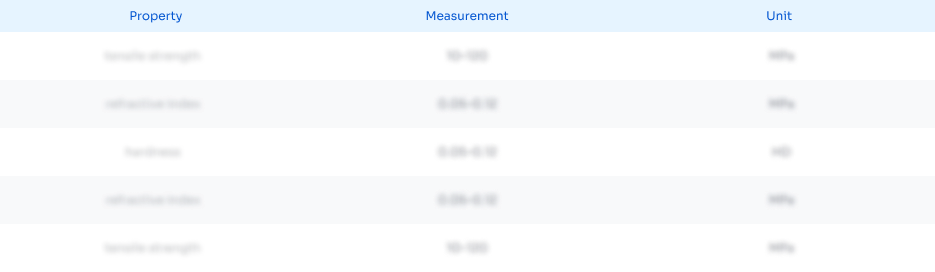
Abstract
Description
Claims
Application Information

- Generate Ideas
- Intellectual Property
- Life Sciences
- Materials
- Tech Scout
- Unparalleled Data Quality
- Higher Quality Content
- 60% Fewer Hallucinations
Browse by: Latest US Patents, China's latest patents, Technical Efficacy Thesaurus, Application Domain, Technology Topic, Popular Technical Reports.
© 2025 PatSnap. All rights reserved.Legal|Privacy policy|Modern Slavery Act Transparency Statement|Sitemap|About US| Contact US: help@patsnap.com