Aluminum alloy section bar anode oxidation surface processing process and processing tank device
An aluminum alloy profile, anodic oxidation technology, applied in the direction of anodic oxidation, etc., can solve the problems of short resin regeneration cycle, high water consumption, etc., achieve the effect of reducing oxidation time, reducing discharge treatment, and increasing the speed of oxidation film formation
- Summary
- Abstract
- Description
- Claims
- Application Information
AI Technical Summary
Problems solved by technology
Method used
Image
Examples
Embodiment 1
[0030] Anodic oxidation process of the present invention and prior art comparative experiment
[0031] 1. The tank solution of the technique of the present invention is composed of: free H 2 SO 4 , 170g / L, Al 3+ , 17g / L, glycerin 1% (w / w), glycolic acid 4% (w / w), anodized with microporous air stirring.
[0032] 2. The bath solution of prior art is composed: free H 2 SO 4 , 170g / L, Al 3+ , 17g / L.
[0033] Through five groups of experiments in the prior art and six groups of experiments in the present invention, the experimental results are shown in Table 1.
[0034] Table 1 The present invention and prior art comparison experiment result
[0035] Table 1 shows that the process of the present invention shortens the oxidation time by nearly 10 minutes compared with the prior art, and the work efficiency is obviously improved.
Embodiment 2
[0037] Effect of microporous air agitation on oxide film
[0038] Bath composition: free H 2 SO 4 , 170g / L, Al 3+ ≤20g / L, glycerin 2% (w / w), lactic acid 3% (w / w), oxidation temperature 30°C, current density 1.4A / dm 2 , the oxidation time was 24 minutes, and the results are shown in Table 2.
[0039] Table 2 Effect of Microporous Stirring on Oxide Film
[0040] Stirring
[0041] Table 2 shows that microporous agitation can increase the conversion coefficient K value of the oxide film by more than 10% compared with no agitation, and can also increase the wear resistance coefficient of the film layer.
Embodiment 3
[0043] The composition of the bath solution is: free H 2 SO 4 , 170g / L, Al 3+ ≤20g / L, lactic acid 4% (w / w), ethylene glycol 3% (w / w), stirred with microporous air, temperature 35°C, current density 2.6A / dm 2 , Oxidized for 18 minutes to obtain a film thickness of 12 microns.
PUM
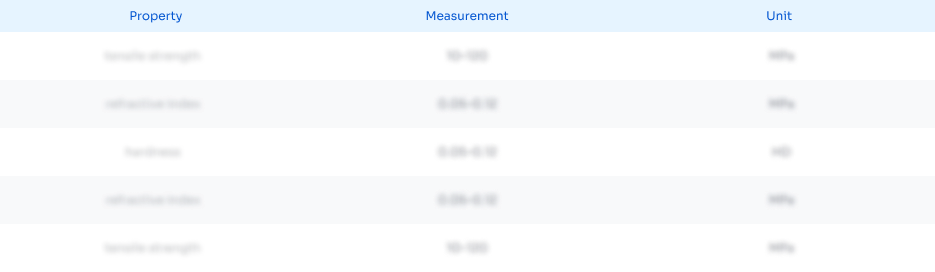
Abstract
Description
Claims
Application Information

- R&D
- Intellectual Property
- Life Sciences
- Materials
- Tech Scout
- Unparalleled Data Quality
- Higher Quality Content
- 60% Fewer Hallucinations
Browse by: Latest US Patents, China's latest patents, Technical Efficacy Thesaurus, Application Domain, Technology Topic, Popular Technical Reports.
© 2025 PatSnap. All rights reserved.Legal|Privacy policy|Modern Slavery Act Transparency Statement|Sitemap|About US| Contact US: help@patsnap.com