Polyaniline/graphene oxide nanofiber composite material, and preparation method and application of composite material
A nanofiber and composite material technology, applied in the direction of hybrid capacitor electrodes, etc., can solve the problems of low specific capacitance and poor electrochemical cycle stability, and achieve the effects of high specific capacitance, simple preparation process, and excellent electrochemical cycle stability.
- Summary
- Abstract
- Description
- Claims
- Application Information
AI Technical Summary
Problems solved by technology
Method used
Image
Examples
Embodiment 1
[0018] (1) Add 0.15 g GONF to 150 mL deionized water and sonicate for 45 min at room temperature to prepare a dispersion of GONF. Add 8 g of cobalt chloride to the above dispersion, and mechanically stir for 90 min at room temperature. The product was washed repeatedly with deionized water until the filtrate was colorless, and then freeze-dried at -50 °C for 48 h to prepare Co 2+ -GONF.
[0019] (2) Add 0.15 g Co 2+ -GONF was added to 250 mL of 1 mol / L hydrochloric acid aqueous solution, and sonicated for 45 min at room temperature to prepare Co 2+ - Dispersion of GONF. Add 2.5 g of aniline to the above dispersion, stir magnetically at room temperature for 45 min to prepare mixed solution I; add 7 g APS to 35 mL of 1 mol / L hydrochloric acid aqueous solution, and stir magnetically at room temperature for 15 min to prepare mixed solution II ; Add the mixed solution II to the mixed solution I drop by drop at a rate of 15 drops / min, and react with magnetic stirring at 2 °C for...
Embodiment 2
[0023] (1) Add 0.1 g GONF to 100 mL deionized water and sonicate for 30 min at room temperature to prepare GONF dispersion. Add 3 g of cobalt chloride to the above dispersion, and stir mechanically at room temperature for 60 min. The product was washed repeatedly with deionized water until the filtrate was colorless, and then freeze-dried at -50 °C for 48 h to prepare Co 2+ -GONF.
[0024] (2) Add 0.1 g Co 2+ -GONF was added to 150 mL of 1 mol / L hydrochloric acid aqueous solution, and sonicated for 30 min at room temperature to prepare Co 2+- Dispersion of GONF. Add 1 g of aniline to the above dispersion and stir magnetically for 30 min at room temperature to prepare mixed solution I; add 2 g APS to 20 mL of 1 mol / L hydrochloric acid aqueous solution and stir magnetically for 5 min at room temperature to prepare mixed solution II ; Add the mixed solution II to the mixed solution I dropwise at a rate of 10 drops / min, and react with magnetic stirring at 0 °C for 24 h. h, pr...
Embodiment 3
[0026] (1) Add 0.2 g GONF to 200 mL deionized water and sonicate for 60 min at room temperature to prepare GONF dispersion. Add 12 g of cobalt chloride to the above dispersion, and stir mechanically at room temperature for 120 min. The product was washed repeatedly with deionized water until the filtrate was colorless, and then freeze-dried at -50 °C for 48 h to prepare Co 2+ -GONF.
[0027] (2) Add 0.2 g Co 2+ -GONF was added to 300 mL of 1 mol / L hydrochloric acid aqueous solution, and sonicated at room temperature for 60 min to prepare Co 2+ - Dispersion of GONF. Add 4 g of aniline to the above dispersion, stir magnetically at room temperature for 60 min to prepare mixed solution I; add 12 g APS to 50 mL of 1 mol / L hydrochloric acid aqueous solution, and stir magnetically at room temperature for 20 min to prepare mixed solution II ; Add the mixed solution II to the mixed solution I drop by drop at a rate of 20 drops / min, and react with magnetic stirring at 5 °C for 12 h,...
PUM
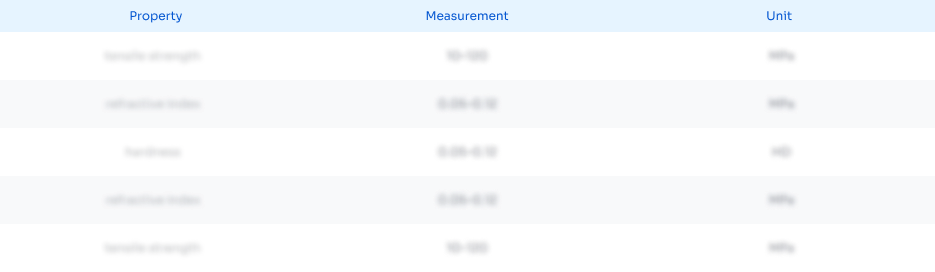
Abstract
Description
Claims
Application Information

- Generate Ideas
- Intellectual Property
- Life Sciences
- Materials
- Tech Scout
- Unparalleled Data Quality
- Higher Quality Content
- 60% Fewer Hallucinations
Browse by: Latest US Patents, China's latest patents, Technical Efficacy Thesaurus, Application Domain, Technology Topic, Popular Technical Reports.
© 2025 PatSnap. All rights reserved.Legal|Privacy policy|Modern Slavery Act Transparency Statement|Sitemap|About US| Contact US: help@patsnap.com