A kind of supported metal catalyst and its preparation method and application
A metal catalyst and supported technology, which is applied in the field of preparation of supported metal catalysts, can solve problems such as uneconomical routes, difficult post-processing, and insufficient green processes
- Summary
- Abstract
- Description
- Claims
- Application Information
AI Technical Summary
Problems solved by technology
Method used
Examples
Embodiment 1
[0017] 1. Preparation of catalyst 3%Cu-3%Ni-0.2%Pd / ZSM-5: Weigh 1.49g Ni(NO 3 ) 2 ·6H 2 O and 1.14gCu(NO 3 )·3H 2 O was added to a 250ml beaker, 3ml of deionized water was added, then stirred and dissolved at room temperature, then 0.2ml of pre-configured chloropalladium acid solution (concentration of 0.1g / ml) was added, and finally 10g of ZSM-5 (NKF -5-80HW) molecular sieves, after the feeding is completed, place it at room temperature and stir for 24 hours, put it in a 110ºC oven and dry it for 12 hours. %Cu-3%Ni-0.2%Pd / ZSM-5 (Cu and Ni content are both 3%, Pd content is 0.2%) catalyst;
[0018] 2. Joint production of 1-butylpyrrolidine, 1-(2-butene)pyrrolidine and 1-(3-butene)pyrrolidine: accurately weigh 18g of 1,4-butanediol, and the concentration of 6.8g is 25 % ammonia solution, 1.8g 3%Cu-3%Ni-0.2%Pd / ZSM-5 catalyst, add to 100mL reactor, use N 2 Evacuate the air before placing the H 2 Pressurize to 4Mpa and fill the reactor, set the reaction temperature to 300ºC...
Embodiment 2
[0020] 1. Preparation of catalyst 3%Cu-3%Ni / ZSM-5: Weigh 1.49g Ni(NO 3 ) 2 ·6H 2 O and 1.14g Cu(NO 3 )·3H 2 Add O into a 250ml beaker, add 3ml of deionized water, then stir to dissolve at room temperature, then slowly add 10g of ZSM-5 (NKF-5-80HW) molecular sieve, after the addition is completed, stir at room temperature for 24 hours, and put it in 110ºC Dry in an oven for 12 hours. After drying, roast in a muffle furnace at 500ºC for 3 hours, and reduce in a reduction furnace with hydrogen at 300ºC for 3 hours to obtain a catalyst 3%Cu-3%Ni / ZSM-5 (both Cu and Ni content are 3%) ;
[0021] 2. Joint production of 1-butylpyrrolidine, 1-(2-butene)pyrrolidine and 1-(3-butene)pyrrolidine: accurately weigh 18g of 1,4-butanediol, 1.8g of 3% Cu -3%Ni / ZSM-5 catalyst, put into 100mL reactor, use N 2 Evacuate the air, fill with 1.7g ammonia, and then add H 2 Pressurize to 4Mpa and fill the reactor, set the reaction temperature to 300ºC, and react for 4 hours; after the reaction, t...
Embodiment 3
[0023] 1. Catalyst preparation: weigh 1.49g Ni(NO 3) 2 ·6H 2 O and 1.14g Cu(NO 3 )·3H 2 O was added to a 250ml beaker, 3ml of deionized water was added, then stirred and dissolved at room temperature, then 0.5ml of a pre-configured chloropalladium acid solution (concentration of 0.1g / ml) was added, and finally 10g of ZSM-5 (NKF -5-80HW) molecular sieves, after the feeding is completed, stir at room temperature for 24 hours, put it in a 110ºC oven and dry it for 12 hours, after drying, roast it in a muffle furnace at 500ºC for 3 hours, and reduce it in a reduction furnace with hydrogen at 300ºC for 3 hours to obtain a catalyst 3%Cu-3%Ni-0.5%Pd / ZSM-5 (Cu and Ni content are both 3%, Pd content is 0.5%);
[0024] 2. Joint production of 1-butylpyrrolidine, 1-(2-butene)pyrrolidine and 1-(3-butene)pyrrolidine: accurately weigh 18g of 1,4-butanediol, and the concentration of 6.8g is 25 % ammonia solution, 1.8g 3%Cu-3%Ni-0.5%Pd / ZSM-5 catalyst, with N 2 Evacuate the air before pla...
PUM
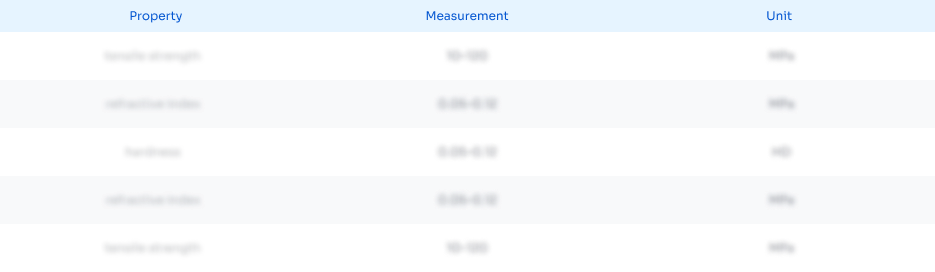
Abstract
Description
Claims
Application Information

- R&D
- Intellectual Property
- Life Sciences
- Materials
- Tech Scout
- Unparalleled Data Quality
- Higher Quality Content
- 60% Fewer Hallucinations
Browse by: Latest US Patents, China's latest patents, Technical Efficacy Thesaurus, Application Domain, Technology Topic, Popular Technical Reports.
© 2025 PatSnap. All rights reserved.Legal|Privacy policy|Modern Slavery Act Transparency Statement|Sitemap|About US| Contact US: help@patsnap.com