Efficient recovery method of elementary substance zinc in zinc smelting tail gas of electric furnace
A recovery method and electric furnace smelting technology, which is applied in the field of efficient recovery of elemental zinc in the tail gas of electric furnace zinc smelting, can solve problems such as equipment damage, pipeline blockage, and low recovery efficiency, achieve efficient recovery, prevent zinc elemental oxidation, and increase surface tension big effect
- Summary
- Abstract
- Description
- Claims
- Application Information
AI Technical Summary
Problems solved by technology
Method used
Examples
Embodiment 1
[0024] The flue gas volume of zinc smelting tail gas in a factory is 15000 m 3 / h, the temperature range of the tail gas after the zinc is collected by the splash condenser is 400-450 ℃
[0025] (1) Prepare a quenched salt solution, dissolve industrial-grade NaCl in water to prepare a salt solution, and the mass concentration of the prepared salt NaCl solution is 12%.
[0026] (2) The tail gas from the electric furnace zinc smelting is passed to the spray tower through the conveying pipeline. Use the NaCl salt solution prepared in step (1) to quench the zinc smelting tail gas by using the washing tower, which is an empty tower. The gas flow velocity in the tower is 1.2 m / s, and the spray density is 17 m 3 / (m 2 h) The gas residence time is 8 s, and the liquid-gas ratio is 4 L / m 3 . After being quenched by the quenching salt solution, the temperature of the zinc smelting tail gas is 32-38°C, and the average recovery rate of zinc in the tail gas is 99.2%.
[0027] (3) The ...
Embodiment 2
[0030] The exhaust gas volume of the electric furnace zinc smelting in a factory is 8000 m 3 / h, the temperature range of the tail gas after the zinc is collected by the splash condenser is 440-480 ℃
[0031] (1) Prepare a quenched salt solution, dissolve industrial-grade KCl in water to prepare a salt solution, and the mass concentration of the prepared salt KCl solution is 15%.
[0032] (2) The tail gas from the electric furnace zinc smelting is passed to the spray tower through the conveying pipeline. Use the KCl salt solution prepared in step (1) to quench the zinc smelting tail gas by using the washing tower, which is an empty tower. The gas flow velocity in the tower is 0.8 m / s, and the spray density is 25 m 3 / (m 2 h) The gas residence time is 11 s, and the liquid-gas ratio is 3.5 L / m 3 . After being quenched by the quenching salt solution, the temperature of the zinc smelting tail gas is 25-35 °C, and the average recovery rate of zinc in the tail gas is 99.6%.
...
Embodiment 3
[0036] The flue gas volume of zinc smelting tail gas in a factory is 26000 m 3 / h, the temperature range of the tail gas after the zinc is collected by the splash condenser is 480-520 ℃
[0037] (1) Prepare a quenched salt solution, dissolve industrial-grade NaCl in water to prepare a salt solution, and the mass concentration of the prepared salt NaCl solution is 13%.
[0038] (2) The tail gas from the electric furnace zinc smelting is passed to the spray tower through the conveying pipeline. Use the NaCl salt solution prepared in step (1) to quench the zinc smelting tail gas by using the scrubber. The scrubber is an empty column and perform secondary scrubbing and quenching. The gas velocity in the tower is 1.5 m / s, and the spray density is 25 m 3 / (m 2 h), the residence time of each scrubber is 7s, the total residence time of gas is 14s, and the liquid-gas ratio is 2.5 L / m 3 . After being quenched by the secondary quenching salt solution, the temperature of the zinc sme...
PUM
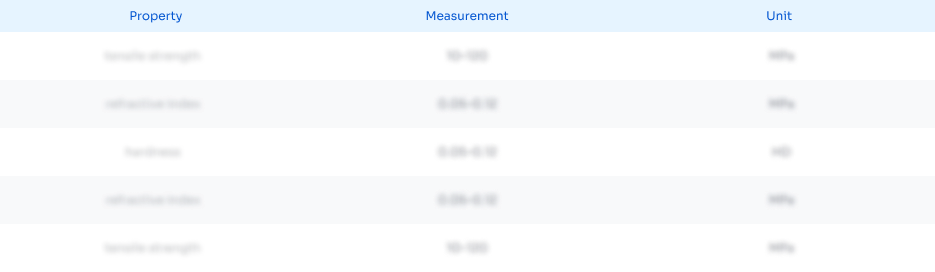
Abstract
Description
Claims
Application Information

- R&D
- Intellectual Property
- Life Sciences
- Materials
- Tech Scout
- Unparalleled Data Quality
- Higher Quality Content
- 60% Fewer Hallucinations
Browse by: Latest US Patents, China's latest patents, Technical Efficacy Thesaurus, Application Domain, Technology Topic, Popular Technical Reports.
© 2025 PatSnap. All rights reserved.Legal|Privacy policy|Modern Slavery Act Transparency Statement|Sitemap|About US| Contact US: help@patsnap.com