A production method for improving the surface quality of low-grade pipeline steel
A technology of surface quality and production method, which is applied in the production field of improving the surface quality of low-grade pipeline steel, can solve the problems of steel plate surface quality deterioration, surface quality deterioration, steel plate erosion, etc., and achieve the elimination of billet grinding and purging treatment , Thickness and melting state are stable, and the effect of improving low temperature toughness
- Summary
- Abstract
- Description
- Claims
- Application Information
AI Technical Summary
Problems solved by technology
Method used
Image
Examples
Embodiment 1
[0056] This embodiment provides a production method for improving the surface quality of low-grade pipeline steel. The steel grade is 5LB, and the blank is 260mm*2070mm section blank, and the product specification is 15mm*3830mm. Specifically:
[0057] S1, its chemical composition and mass percentage are as follows: C: 0.060%~0.080%, Si: 0.20%~0.30%, Mn: 1.20%~1.40%, P≤0.015%, S≤0.0030%, Ni≤0.20%, Nb ≤0.070%, Cr≤0.30%, Mo≤0.15%, Ti: 0.005%~0.02%, N≤0.0050%, Ca: 0.001%~0.003%, Al: 0.010%~0.050%, the balance is Fe and unavoidable impurities;
[0058] S2. The desulfurization station uses lime and magnesium powder for compound desulfurization. After desulfurization, the slag is cleaned. S: 0.0020% in the molten iron, and S: 0.008% after the converter;
[0059] S3. Steelmaking adopts the process route of BOF → LF furnace refining → RH refining → continuous casting. The tapping temperature of the converter is 1668°C, and the tapping is made of pre-melted refining slag + active lim...
Embodiment 2
[0067] This embodiment provides a production method for improving the surface quality of low-grade pipeline steel. The steel grade is X60M, and the blank is 220mm*2070mm section blank, and the product specification is 23.83mm*3890mm. Specifically:
[0068] S1, its chemical composition and mass percentage are as follows: C: 0.040%~0.060%, Si: 0.10%~0.30%, Mn: 1.30%~1.50%, P≤0.015%, S≤0.0030%, Ni≤0.20%, Nb : 0.040%~0.070%, Cr≤0.15%, Mo≤0.15%, Ti: 0.005%~0.02%, N≤0.0050%, Ca: 0.001%~0.003%, Al: 0.010%~0.050%, the balance is Fe and unavoidable impurities;
[0069] S2. The desulfurization station uses lime and magnesium powder for composite desulfurization. After desulfurization, the slag is cleaned. S: 0.0020% in the molten iron, and S: 0.006% after the converter;
[0070] S3. Steelmaking adopts the process route of BOF→LF furnace refining→RH refining→continuous casting. The tapping temperature of the converter is 1653°C, and the tapping is made of pre-melted refining slag + act...
Embodiment 3
[0078] This embodiment provides a production method for improving the surface quality of low-grade pipeline steel. The steel grade is X65M, and the blank is 320mm*2570mm section blank, and the product specification is 27.2mm*3110mm. Specifically:
[0079] S1, its chemical composition and mass percentage are as follows: C: 0.050%~0.070%, Si: 0.15%~0.25%, Mn: 1.40%~1.60%, P≤0.015%, S≤0.0030%, Ni≤0.20%, Nb : 0.030%~0.070%, Cr: 0.15%~0.30%, Mo≤0.15%, Ti: 0.005%~0.02%, N≤0.0050%, Ca: 0.001%~0.003%, Al: 0.010%~0.050%, remainder The amount is Fe and unavoidable impurities;
[0080] S2. The desulfurization station uses lime and magnesium powder for compound desulfurization. After desulfurization, the slag is cleaned. S: 0.0020% in the molten iron, and S: 0.008% after the converter;
[0081] S3. Steelmaking adopts the process route of BOF → LF furnace refining → RH refining → continuous casting. The tapping temperature of the converter is 1669°C, and the tapping is made of pre-melted r...
PUM
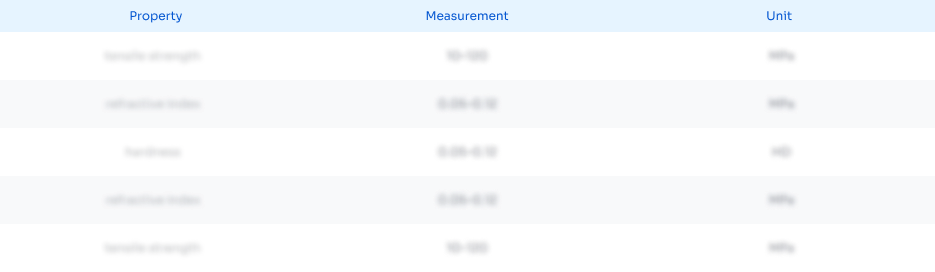
Abstract
Description
Claims
Application Information

- Generate Ideas
- Intellectual Property
- Life Sciences
- Materials
- Tech Scout
- Unparalleled Data Quality
- Higher Quality Content
- 60% Fewer Hallucinations
Browse by: Latest US Patents, China's latest patents, Technical Efficacy Thesaurus, Application Domain, Technology Topic, Popular Technical Reports.
© 2025 PatSnap. All rights reserved.Legal|Privacy policy|Modern Slavery Act Transparency Statement|Sitemap|About US| Contact US: help@patsnap.com