Preparation method of biodegradable polyurethane composite
A composite material and polyurethane technology, applied in the field of polyurethane materials, can solve the problems that polyurethane materials cannot be naturally biodegraded, and achieve the effects of improving biocompatibility, reducing adsorption capacity, and improving hydrophilicity
- Summary
- Abstract
- Description
- Claims
- Application Information
AI Technical Summary
Problems solved by technology
Method used
Image
Examples
Embodiment 1
[0035] Place polyethylene glycol and mint adhesive fiber in a vacuum drying oven, and vacuum-dry and dehydrate at 60°C and 2000 Pa for 10 hours to obtain dehydrated polyethylene glycol and dehydrated mint adhesive fiber, which are weighed in parts by weight, respectively. Measure 10 parts of dehydrated mint adhesive fiber, 10 parts of dehydrated polyethylene glycol, 20 parts of ε-caprolactone, 20 parts of adipic acid, 1 part of butyl titanate, and mix dehydrated mint adhesive fiber, dehydrated polyethylene glycol Put it in a vacuum reaction bottle, keep it at 80°C and 4000Pa for 1 hour, and cool it at room temperature to obtain a mixed system. Add ε-caprolactone, adipic acid, and butyl titanate into the mixed system, and add The gas flow rate was protected by argon, stirred and reacted at 150r / min under the condition of 120°C for 2h, cooled at room temperature to obtain a mint fiber-based polyester copolymer, and then 50 parts by weight of hexamethylene bismuth Isocyanate, 10 ...
Embodiment 2
[0037] Place the polyethylene glycol and mint adhesive fiber in a vacuum drying oven, and vacuum-dry and dehydrate at 70°C and 2500 Pa for 11 hours to obtain dehydrated polyethylene glycol and dehydrated mint adhesive fiber, which are weighed in parts by weight, respectively. Measure 12 parts of dehydrated mint adhesive fiber, 12 parts of dehydrated polyethylene glycol, 25 parts of ε-caprolactone, 22 parts of adipic acid, 2 parts of butyl titanate, and dehydrated mint adhesive fiber, dehydrated polyethylene glycol Put it in a vacuum reaction bottle, keep it under the condition of 90°C and 4500Pa for 1 hour, and cool it at room temperature to obtain a mixed system. The gas flow rate was protected by argon, stirred and reacted at 175r / min under the condition of 130°C for 3h, and cooled at room temperature to obtain a mint fiber-based polyester copolymer, and then 55 parts by weight of hexamethylene di Isocyanate, 15 parts of 1,4-butanediol, hexamethylene diisocyanate, nitrogen p...
Embodiment 3
[0039] Place polyethylene glycol and mint adhesive fiber in a vacuum drying oven, and vacuum-dry and dehydrate at 80°C and 3000 Pa for 12 hours to obtain dehydrated polyethylene glycol and dehydrated mint adhesive fiber, which are weighed in parts by weight, respectively. Measure 15 parts of dehydrated mint adhesive fiber, 15 parts of dehydrated polyethylene glycol, 30 parts of ε-caprolactone, 25 parts of adipic acid, 3 parts of butyl titanate, and dehydrated mint adhesive fiber, dehydrated polyethylene glycol Put it in a vacuum reaction flask, keep it at 100°C and 5000Pa for 2 hours, and cool it at room temperature to obtain a mixed system. Add ε-caprolactone, adipic acid, and butyl titanate into the mixed system, and add The gas flow rate was passed into the protection of argon, stirred and reacted at 200r / min under the condition of 140°C for 4h, and cooled at room temperature to obtain a mint fiber-based polyester copolymer, and then 60 parts by weight of hexamethylene di I...
PUM
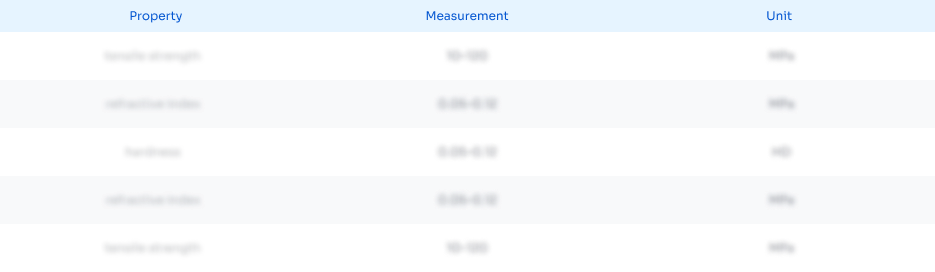
Abstract
Description
Claims
Application Information

- Generate Ideas
- Intellectual Property
- Life Sciences
- Materials
- Tech Scout
- Unparalleled Data Quality
- Higher Quality Content
- 60% Fewer Hallucinations
Browse by: Latest US Patents, China's latest patents, Technical Efficacy Thesaurus, Application Domain, Technology Topic, Popular Technical Reports.
© 2025 PatSnap. All rights reserved.Legal|Privacy policy|Modern Slavery Act Transparency Statement|Sitemap|About US| Contact US: help@patsnap.com